
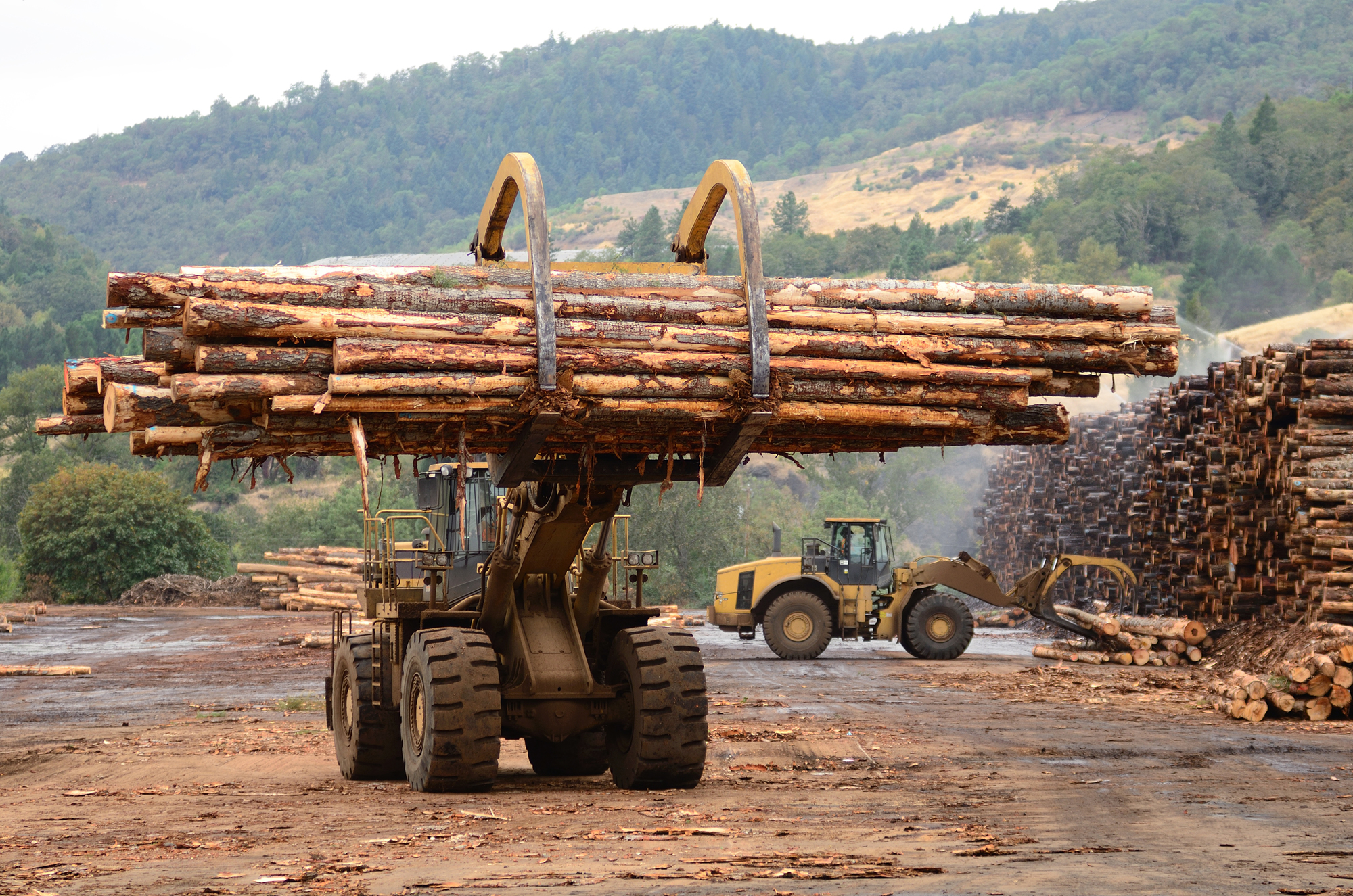
TMP™ Saves 78 Days
This wood-based panel manufacturer had an unpredictable track record with shutdowns and maintenance.
“TMP™ (Theoretical Maximum Performance) planning techniques are now well accepted and are being utilized by general managers throughout our mills. Team members have been trained in what is now accepted as a core skill in our organization. The unique aspect of all three projects is that the plan timelines were initially considered impossible targets by both the equipment suppliers and construction companies involved, yet we achieved success.”
—President and CEO
Context/Challenge
This international producer of wood-based panels, with plants across North America and Europe, asked for RLG’s help to improve the shutdown performance of its North American mills. They had an unpredictable history of success with both shutdowns and maintenance, averaging nearly 20% over plan.
At the start, this client had:
- Shutdowns: For the division to stay competitive, unit costs needed to come down while lumber quality and lumber recovery indicators needed to be improved.
- Low focus and accountability: From leadership to the front line, the organization lacked a cascading focus on key metrics and a guiding ‘north star’ of what good looked like.
- Varying ways of working: Individual leaders and teams worked independently of other teams, rarely following consistent processes and effective use of data and systems.
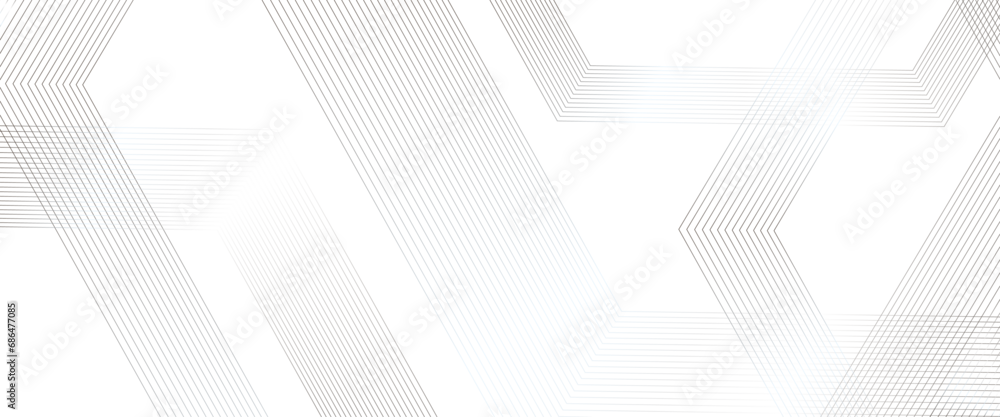
Approach
Beginning with a project mindset and a handful of shutdown and “event” opportunities to target, RLG’s team worked closely with Operations, Maintenance, technical and leadership teams across the many mills.
- Enabled Front Line Involvement: With data, structured problem solving, facilitated optimization sessions, field observation, and After-Action Reviews, everyone had a voice, from the front-line workers and contractors to the top leadership.
- Optimization: Facilitated TMP™ workshops introduced the ideas of “perfect execution” and through optimization of critical path activities, enabled execution of a quality plan through involvement and ownership of all participants.
- Targeting: This team targeted troublesome shutdown events and tasks with inconsistent performance and together built strong, repeatable practices.
Result
The 19 projects after the start of the RLG engagement came within 1% of plan.
- Crews, suppliers, contractors and planning teams were all highly engaged in the process.
- Weekly dryer cleaning time was cut by 49%, achieving durations previously thought impossible.
- An 8-week press rebuild was completed on budget, 20% ahead of baseline with no recordable injuries.
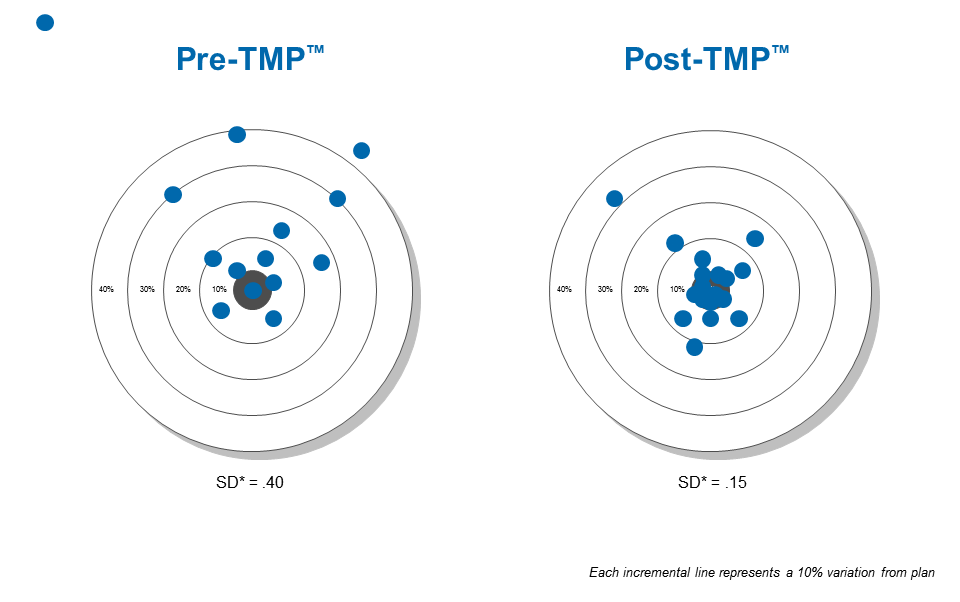
Ready to change the way YOUR business is done?
We would love to learn about your unique challenges. Contact our team for a no-obligations conversation or even a site visit.
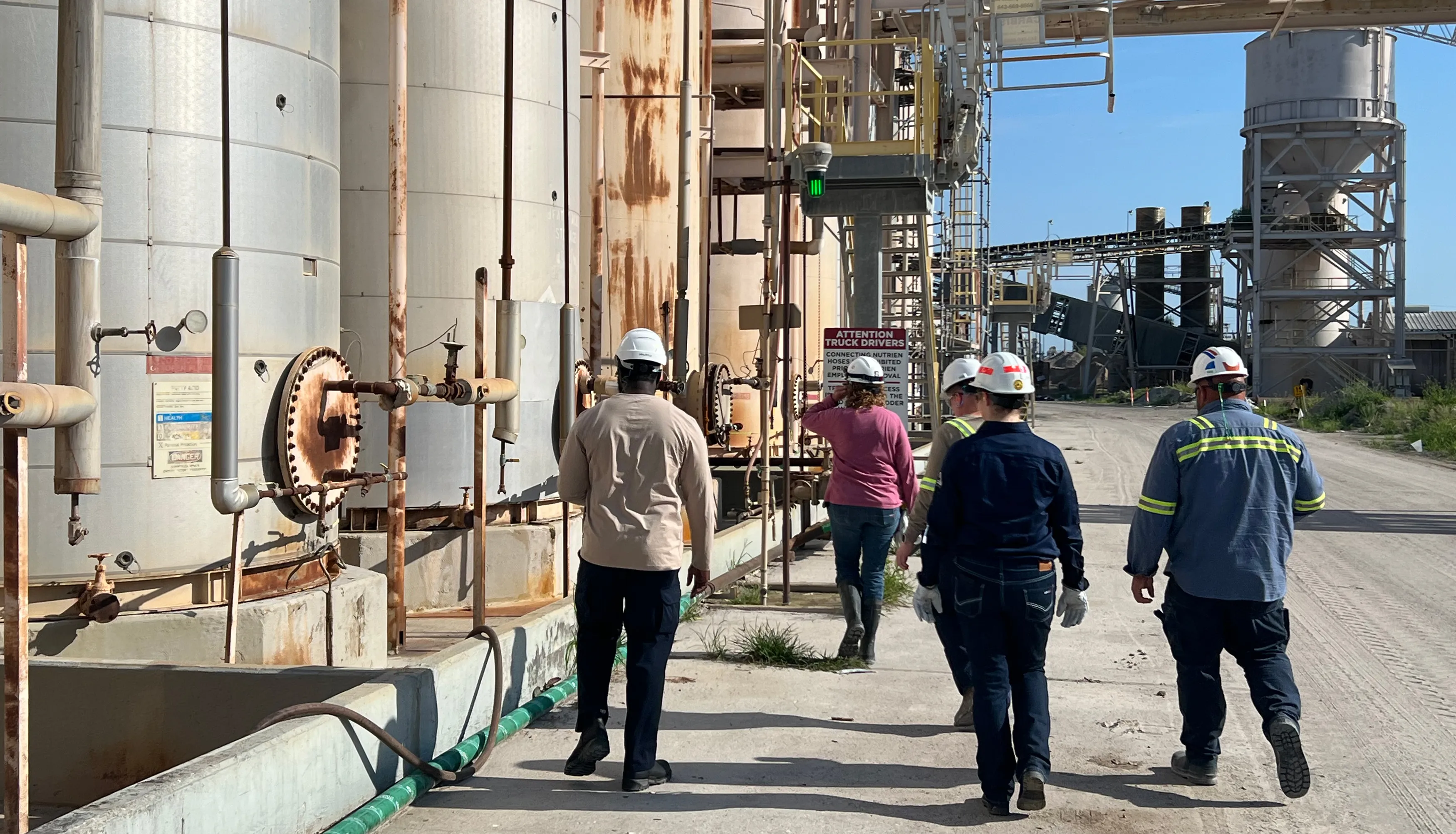