
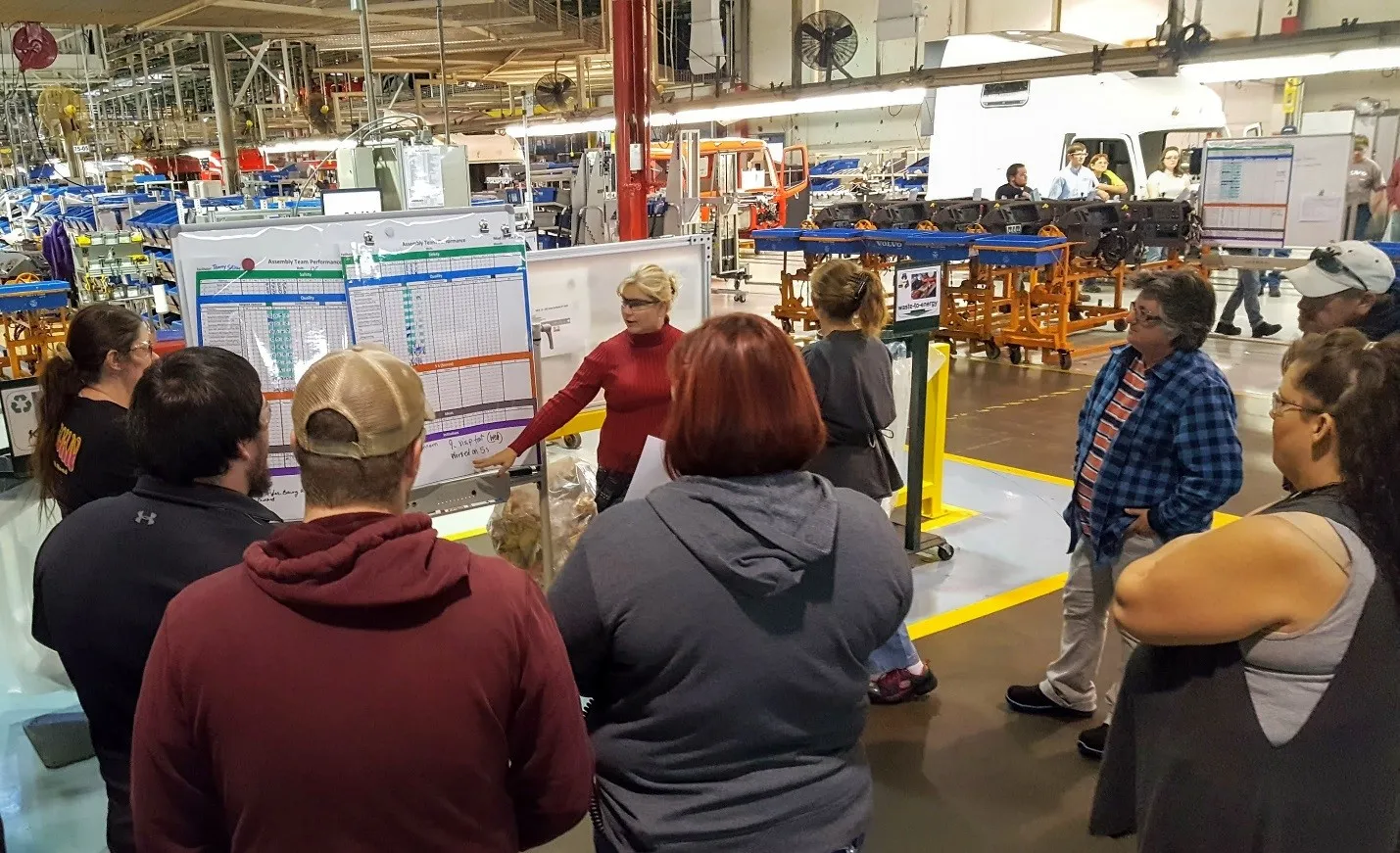
The Road to Sustainable Production Performance
This worldwide auto manufacturer engaged RLG to help implement a systematic production system in their main North American manufacturing plant, achieving significant improvements in frontline engagement and defect reduction.
“We are really starting to see the changes the program is making both with the emphasis on 5S as well as implementing employee ideas and suggestions.”
— Operator, Module 10
Context/Challenge
This large North American manufacturing plant, with over 2,200 skilled trades and assemblers, was deeply engaged in a multi-year continuous improvement journey.
RLG’s initial assessment revealed a significant gap between the documented manufacturing system and the behaviors in practice on the shop floor. Performance awareness and frontline leadership were lacking, and there was little time allocated for team leads to interact with their team. Those interactions that did occur were unstructured and inconsistent, failing to engage floor workers in performance improvement and problem-solving.
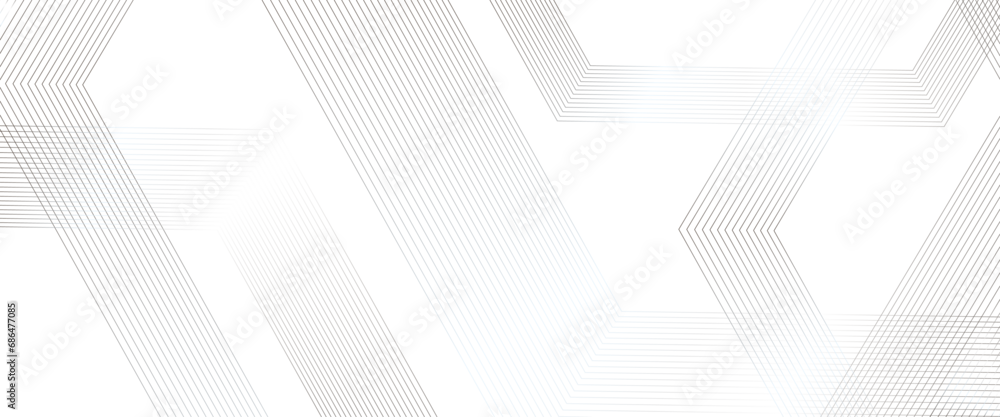
Approach
- Initial Assessment: Identified a significant gap between the documented system and shop floor behaviors, with a lack of performance awareness and frontline leadership.
- Targeted Improvements: To limit scope and test impact, the pilot targeted specific manufacturing lines. Additional scope areas were added as methods were shown effective and employees and team leaders aligned to the approach.
- Improved Planning: Carved out space for team leads and frontline supervisors, developing a daily structure to support long-term goals and implement structured problem-solving tools.
- Guidelines and Systems: Positioned visual management boards in each module to track performance and focus behavior, and provided coaching using leadership scorecards.
- Leadership Engagement: Worked with the senior leadership team on a strategic level, supporting their three-year planning ‘Hoshin Kanri’ strategy deployment process.
- Performance Monitoring: Implemented the Operating Rhythm™ to engage frontline leaders in daily intentional problem-solving and performance improvement.
Result
- Frontline Engagement: Improved by 23%, as measured by the corporate annual global survey.
- Open Defects: Reduced by 56%, achieved through daily intentional problem-solving and engagement from frontline leaders.
- Leadership Capability: Enhanced by 64%, as measured by the RLG FAIR™ Model Assessment.
- Strategic Focus: Drew attention to significant issues around procurement and logistics, which received specific attention in the senior level plans in the following year.
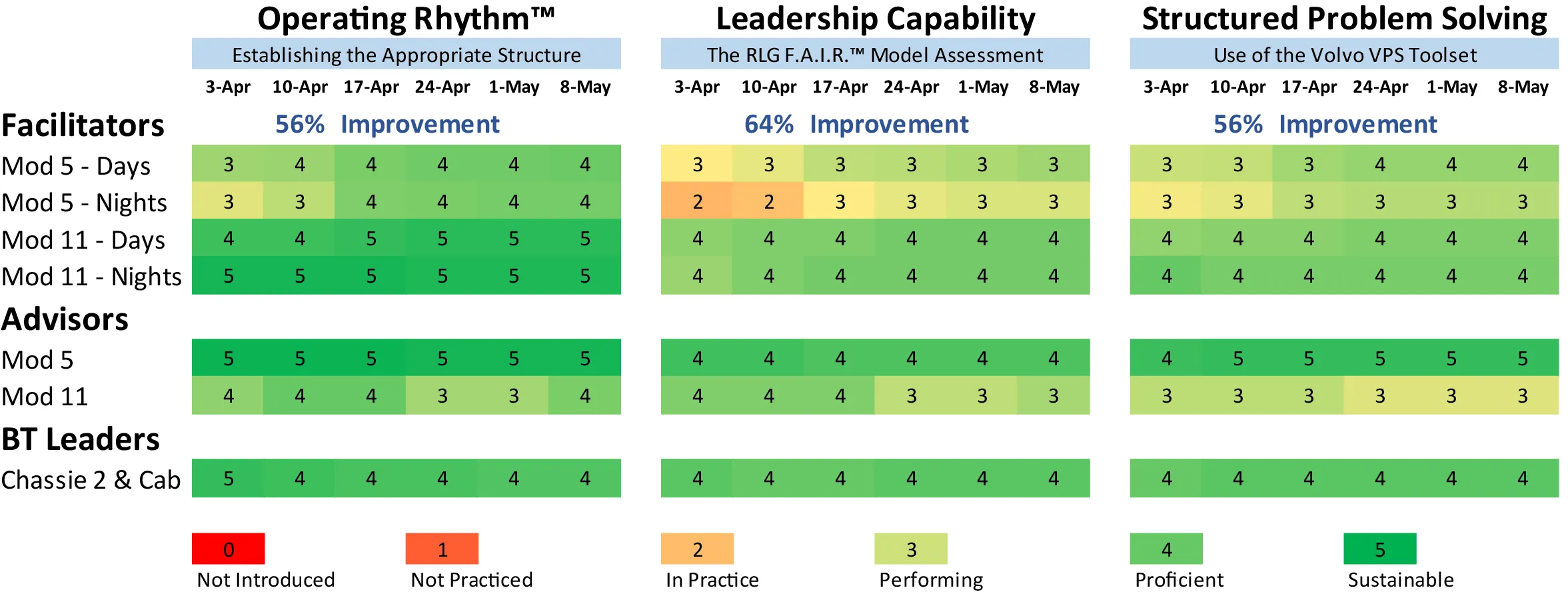
Ready to change the way YOUR business is done?
We would love to learn about your unique challenges. Contact our team for a no-obligations conversation or even a site visit.
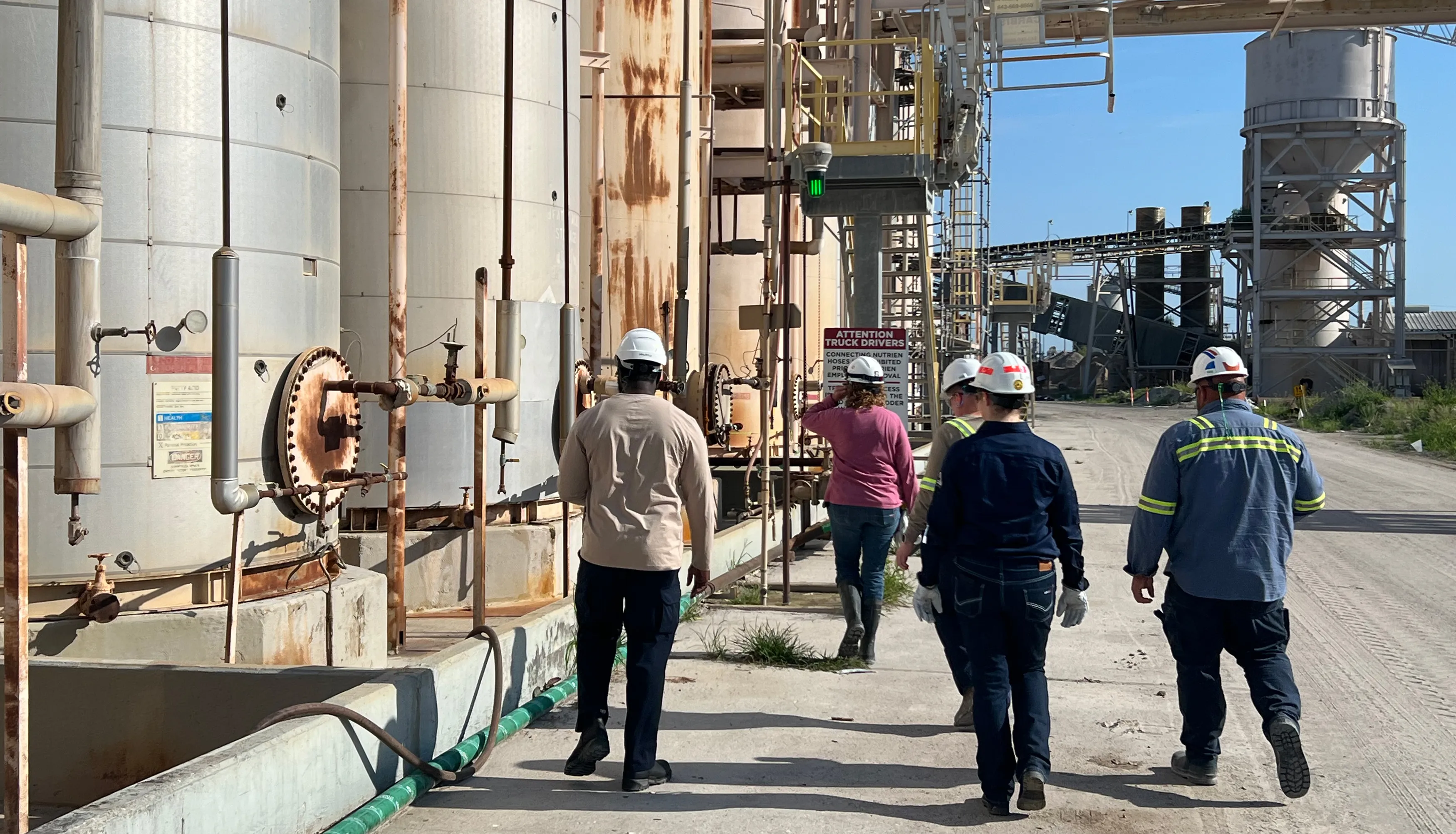