
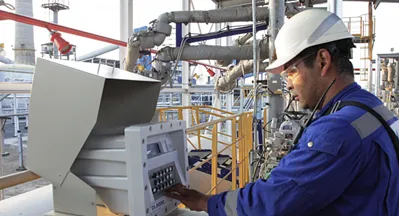
ROx™ project implementation at mid-size refinery
Established the rhythm for communicating results and plans forward at the refinery through refining operations and production area levels.
“I was very excited about the (Business Review) event. It was the first time in my life we discussed those important questions within this group of participants.”
— Crude Distillation Deputy Area Manager
Context/Challenge
Refinery launched a joint project with RLG aiming to introduce and implement systems to increase efficiency within the production process to improve financial efficiency of the refinery by:
- Introducing a structure of aligned and cascading KPIs that is clear and transparent,
- creating a structured system for more efficient interaction at all management levels and production personnel,
- involvement of the workforce in the process of efficiency improvement, and
- improving communications between production and production support services.
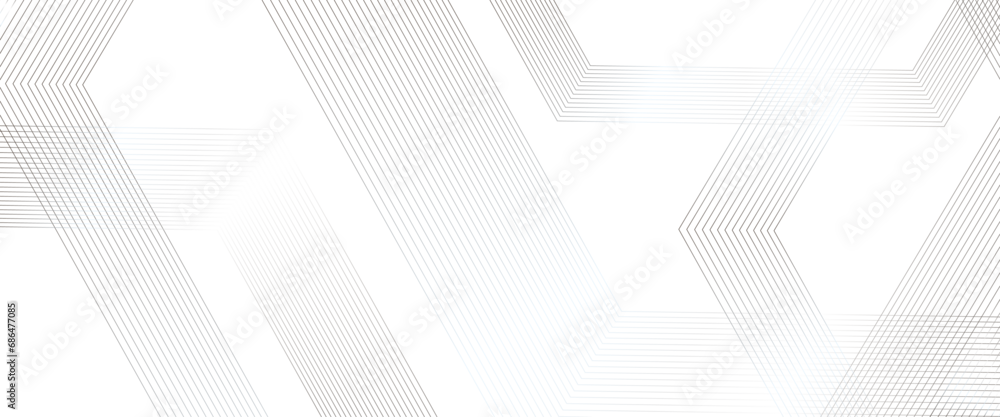
Approach
Initially five major lenses were identified, agreed with the client and implemented. They included:
- Performance - development and introduction of aligned KPIs from the level of the organization management to the level of unit operations shift crew,
- Engagement - introduction of Operating Rhythm™ including Business Reviews for discussion of results to date and planning improvement actions forward at the refinery management, operations management and production units’ levels,
- Integration – improvement of interaction and collaboration of Operations with Maintenance and Reliability organizations,
- Optimization – improvement of refinery margin through specific activities focused on production optimization, product optimization, and reduction of OPEX, and
- Leadership – development of leadership and managerial skills of the project key stakeholders.
Result
During the project:
- The project had a client verified impact of nearly $17 million,
- The refinery set a record by refining 5.38 M tons of oil against a nameplate capacity of 5 M ton of oil a year,
- Average daily plan execution deviation improved from –3.0% to +2.8%,
- Units’ non-productive time reduced by 30%,
- Product loading time (subject to the product specification) reduced by 17%, and
- Overall refinery operational efficiency increased by 37%.
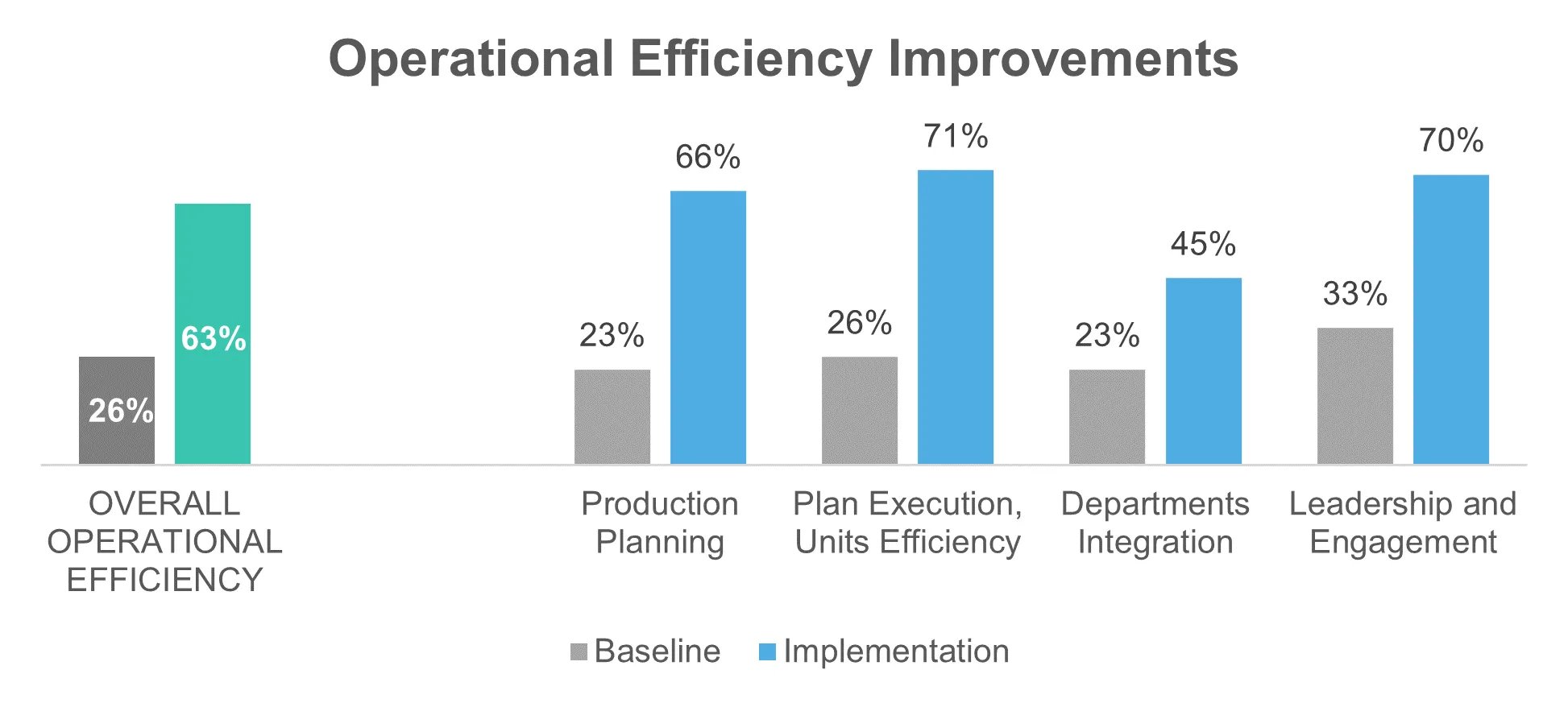
Ready to change the way YOUR business is done?
We would love to learn about your unique challenges. Contact our team for a no-obligations conversation or even a site visit.
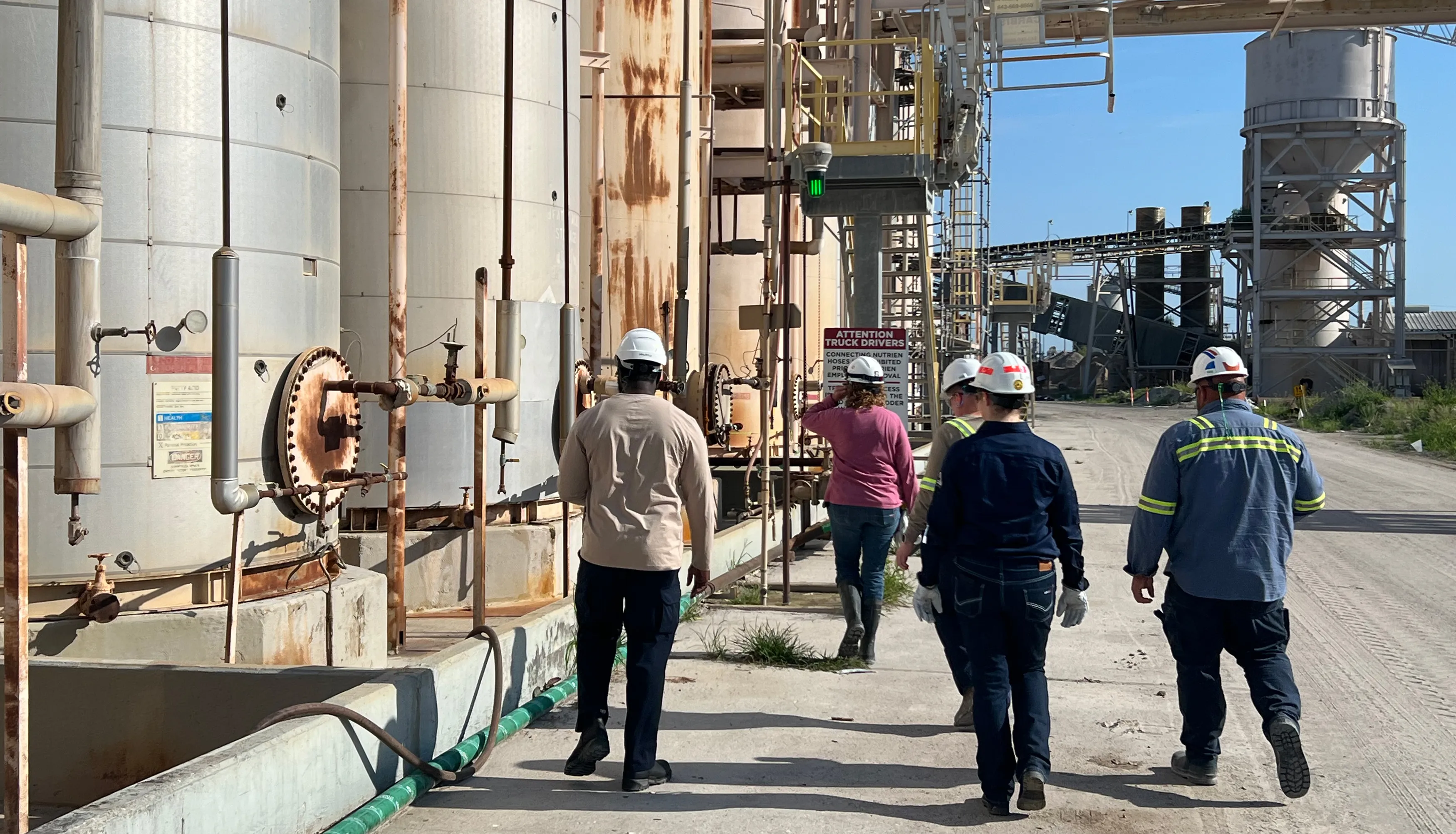