
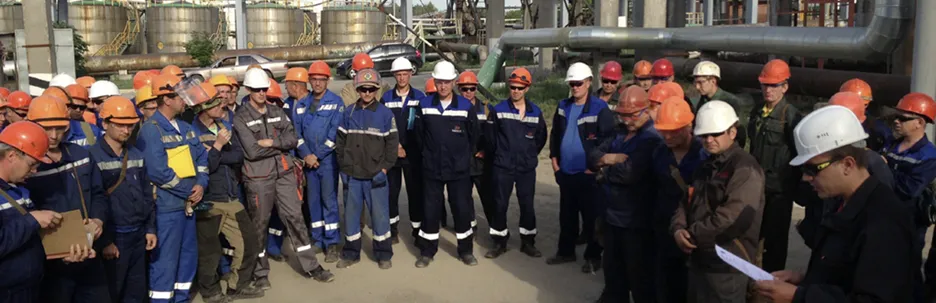
Refinery Turnaround Preparation and Execution
This refinery client implemented a more structured planning and execution process for their turnaround, with a total budget of $90 million and several coinciding capital projects.
“I don’t want this project to be a one-time episode. This is a success that needsto be repeated for the next TAR.”
— General Director of the Refinery (to a visiting delegation of company executives following the successful turnaround result)
Context/Challenge
Our client, one of the largest oil refining companies in Russia, decided to undertake a large-scale modernization and reconstruction of one of its refineries. All work was required to be completed within strictly defined timelines, sequenced with ongoing TAR activities and operational plans across all units of the refinery.
- Work scope. This project was classified as highly complex, as the modernization and reconstruction efforts accounted for over 87% of the total scope of work.
- TAR execution. All previous TARs were carried out with significant deviations from the established timelines. Planning credibility was tarnished, and executive attention was high.
- Procurement. There were significant challenges in procuring the necessary materials and equipment on time, thus early-as-possible planning and procurement was essential.
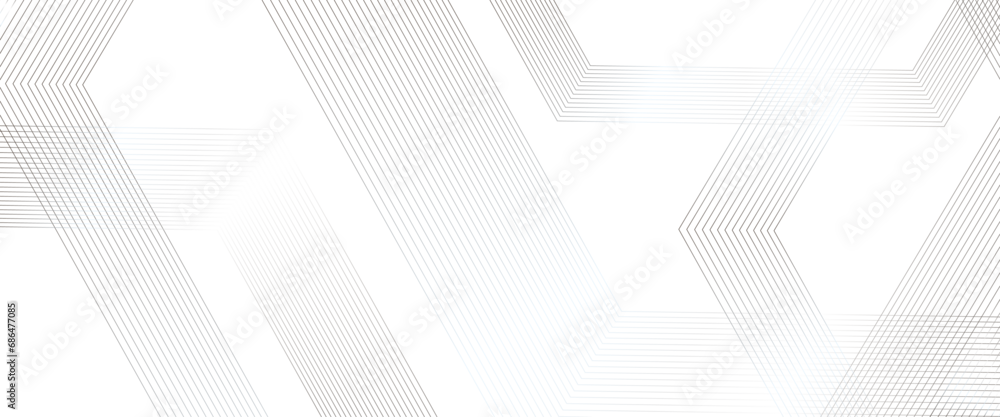
Approach
RLG’s experience and structured approach, together with tools such as Operating Rhythm™ and FAIR™ (Focus-Accountability-Involvement-Response model), were implemented and played a key role in the successful execution of the project.
The most important focus areas were:
- Increasing focus and accountability of all TAR participants through the establishment of working groups. Everyone became clear on the plan and their role in that plan.
- Resolving the majority (up to 85%) of operational issues on the bottom level, avoiding escalation and streamlining decision making.
- Developing leadership and management skills among key players in the process.
Some of the processes developed and handed over to the client were:
- Improved scheduling rigor, including Gantt chart preparation and execution schedules on an hourly basis for the Refinery units.
- Schedule optimization to identify pre-work, clearer scopes, shorter duration, reduced risk and more efficient ways of working.
- Operating and communication processes for Refinery personnel and contractors.
- Cascading KPIs up, down and across the turnaround and operating organization.
- One-page KPI reports for regular (daily, weekly, monthly) tracking the work progress and trends.
Result
- 100% of pre-TAR works and 98.5% delivery of equipment/materials were completed before the start of the turnaround.
- The new approach implemented for this turnaround project was officially recognised as the Best Practice within this client’s Downstream and ordered by the Vice-President to cascade across all their refineries.
- Almost 90% of operational issues were resolved by front-liners without escalating to the top management (vs. 10% in last TAR).
- This TAR was completed one day ahead of schedule and no LTAs which resulted in an economic impact of $31.7 million.
- The refinery visbreaking section was recovered from fire damage into operation 107 days ahead of schedule, which led to a financial impact of $7 million.
- The refinery visbreaking section was reconstructed 132 days ahead of schedule, which resulted in a financial impact of $4.6 million.
- Cumulative dollar impact of $43.3 million amounted to a 16:1 ROI for the client.
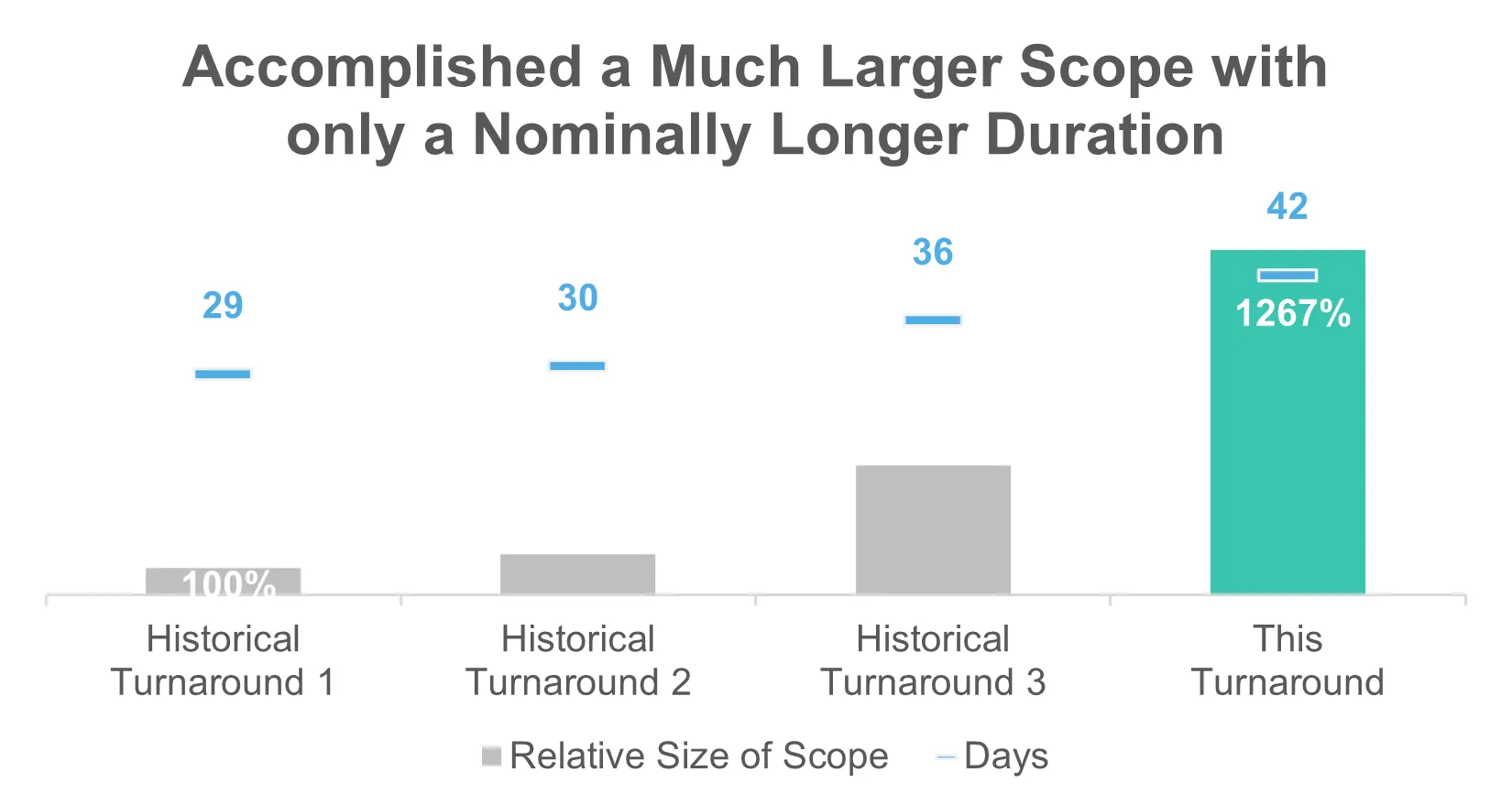
Ready to change the way YOUR business is done?
We would love to learn about your unique challenges. Contact our team for a no-obligations conversation or even a site visit.
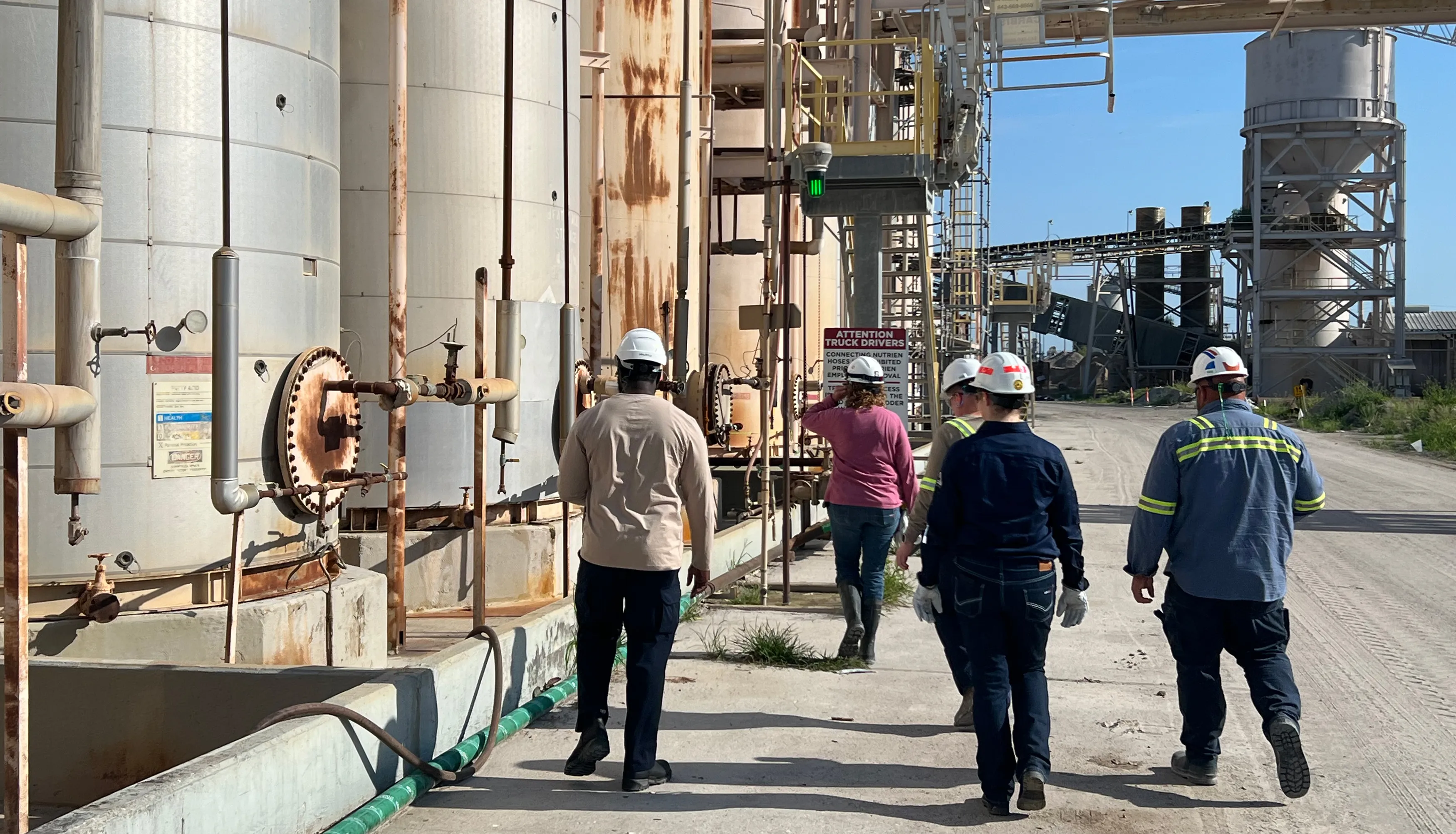