
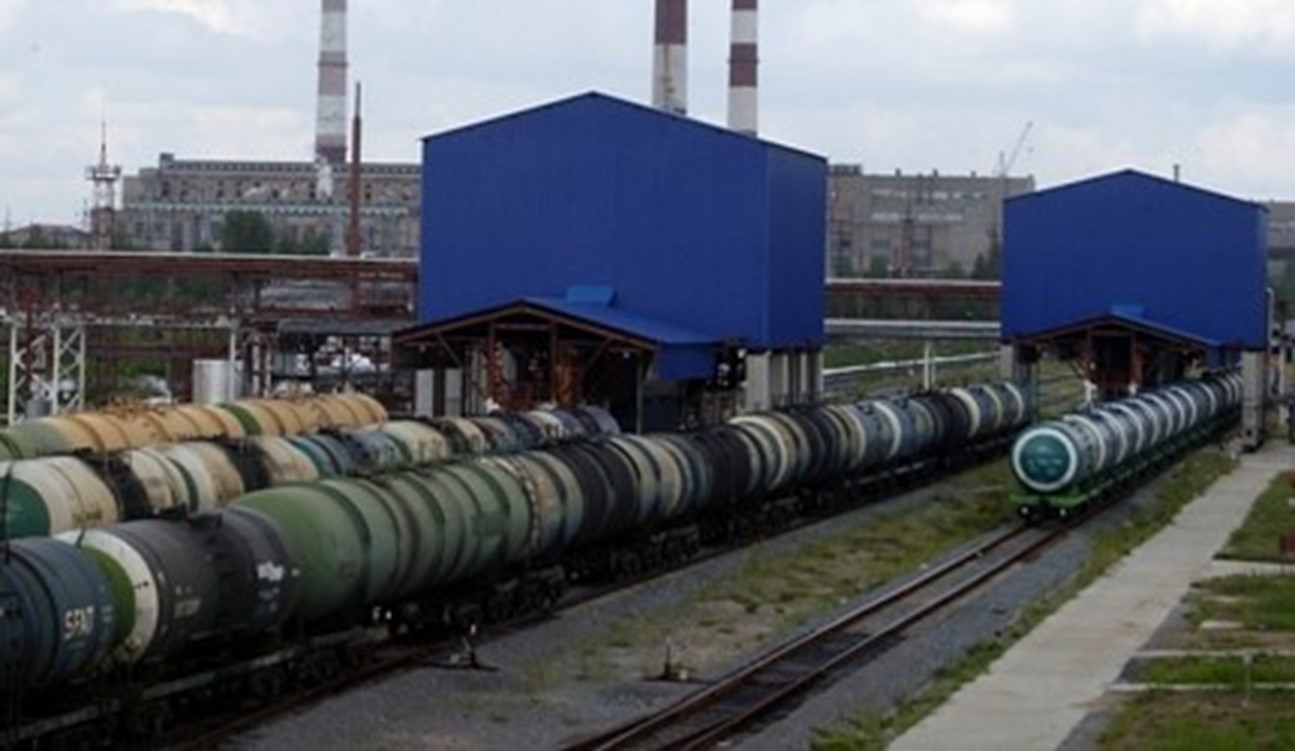
Refinery Rail Logistics
This refinery scored gains in productivity, throughput, process safety and environment.
“In addition to getting fantastic bottom-line results, RLG’s methodology and instruments helped us change the way we communicate. The whole culture of our communication changed dramatically, both among different departments and divisions, and within our Corporate Headquarters.”
— Vice President, Refining Operations
Context/Challenge
Management at this midsized refinery identified a strategic debottlenecking opportunity to improve efficiency and capacity of rail tank-car loading and shipping.
Their initial assessment called for improvements in all aspects of shipping and loading at their refinery; however, critical improvements were needed in utilization and performance in two spot loading facilities to comply with the Corporate Integrity Strategy. These stated that “… for all light products, railcar loading must be done by means of hermetically sealed facilities with vapour recovery technology, particularly for gasoline products.”
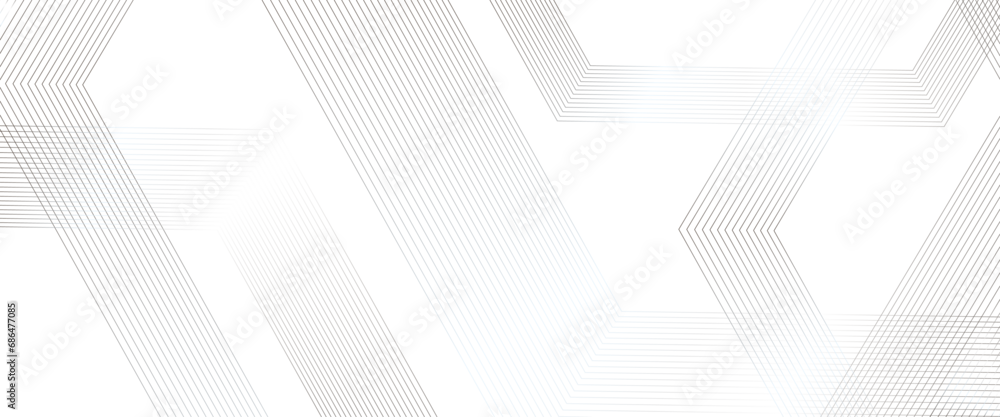
Approach
The solution was not to be found in a single initiative focused only on the ELINs; rather, this needed an integrated strategy, involving multiple entities: the rail operator, the client head-office, and refinery support operations. In fact, multiple departments within those entities carried part of the solution, where RLG navigated and brought together the client’s Maintenance Shops, Loadout Department, Production with Blending Operations, and Production/Shipping Planning/Scheduling. What resulted were an agreed upon approach to infrastructure, equipment, business processes, documentation flow, and an aligned approach to implementing all the opportunities.
What it didn’t involve was huge sums of money. The solution had more to do with working together in better cooperation and planning.
Result
This cultural change was the driving force that made this project a real success:
- 78% of light products were compliant with the Integrity Strategy, more than double the starting baseline. The entire volume of Naptha and most grades of gasoline were loaded via spot loading facilities. Improvements continued after RLG’s departure.
- Vapour Recovery Unit, as a part of the spot loading facilities infrastructure, was recommissioned to operate 24x7 and generated >$2 million each year without any capital investment
- Process and work efficiency improvements enabled spot loading facilities’ throughput to produce and ship on average 27,000 tons/month more gasoline.
- Blending station process and operational improvements enabled $14.1 million higher earnings from increased gasoline production with zero CAPEX
- Spot loading facilities removed a major HSE risk by eliminating open-air gasoline loading, with zero CAPEX. This also enabled $2 million in savings on fines and fees payable to the railway operator
This project was a tremendous achievement for this client, enabling both commercial and regulatory success, and was culturally significant across many organizational boundaries.
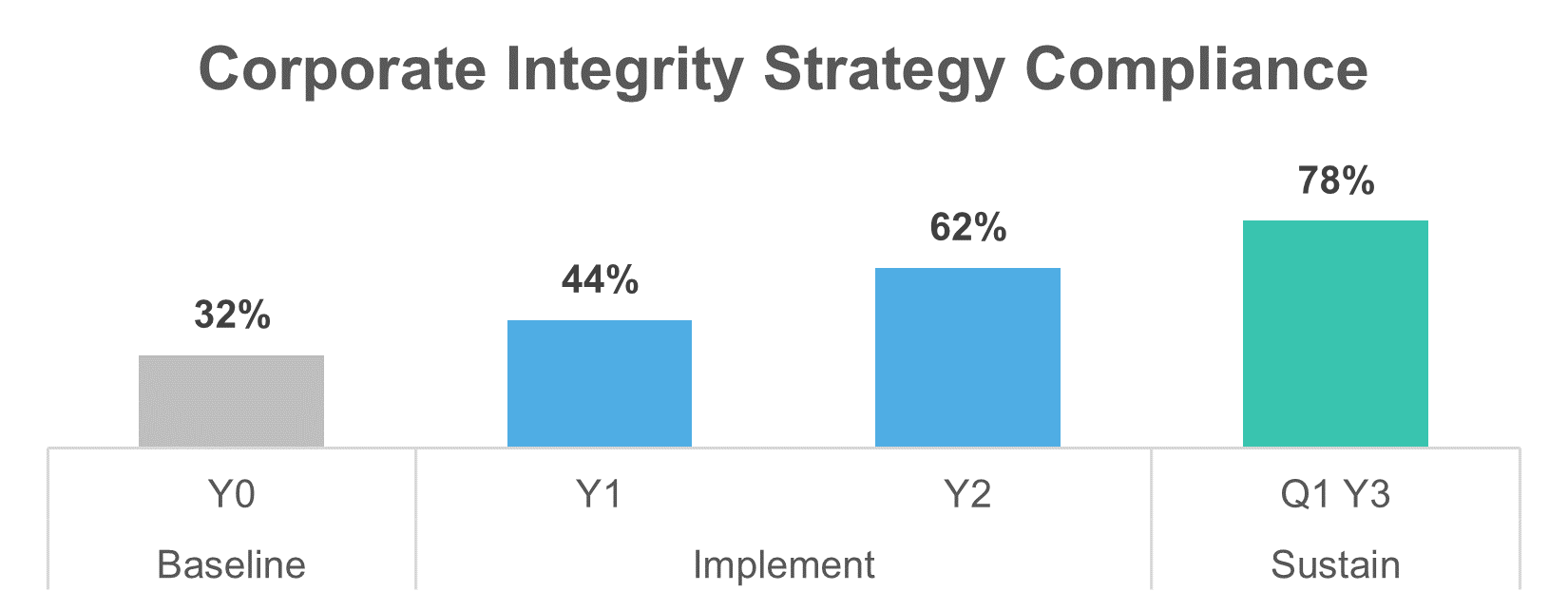
Ready to change the way YOUR business is done?
We would love to learn about your unique challenges. Contact our team for a no-obligations conversation or even a site visit.
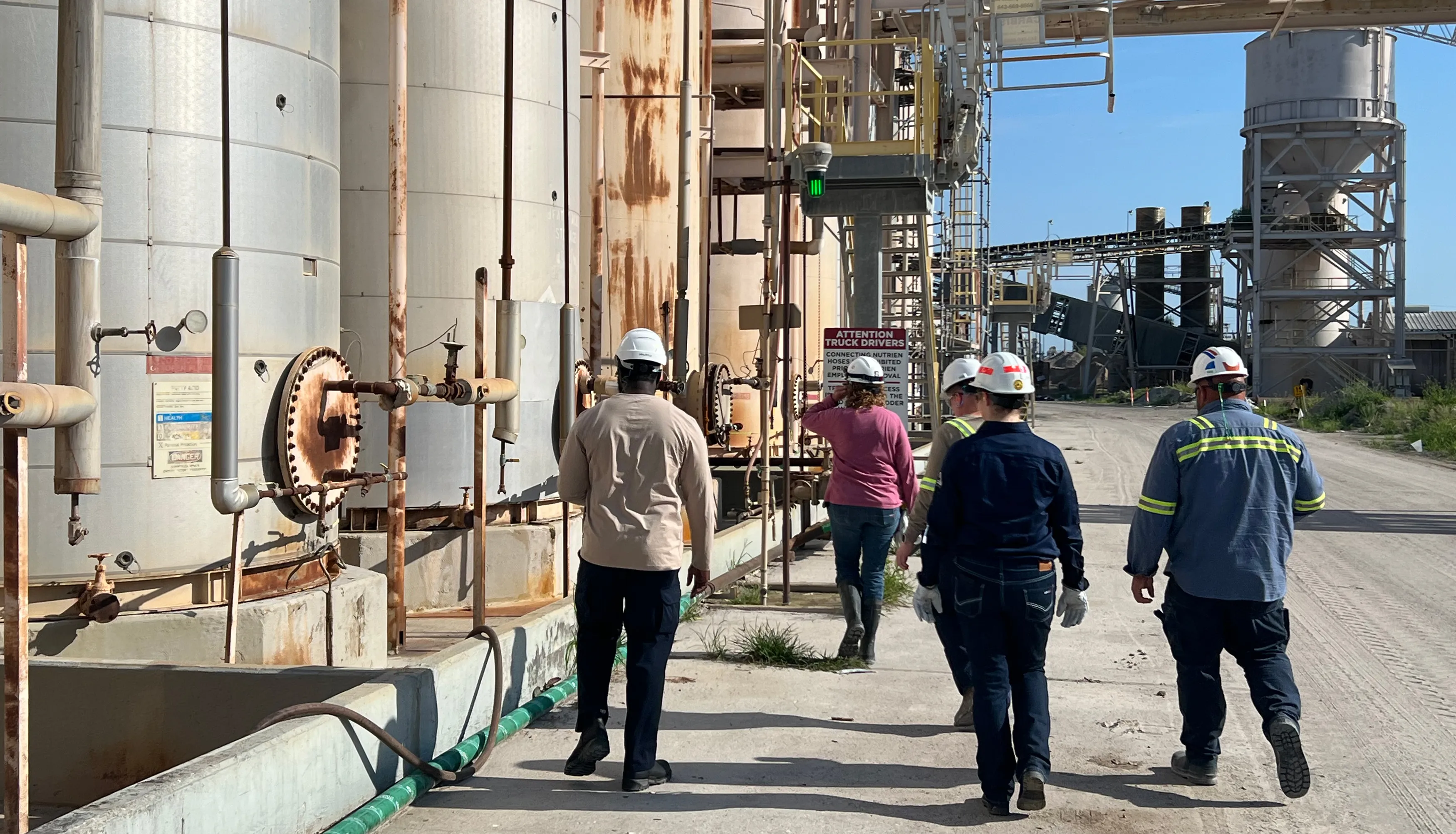