

Fertilizer Manufacturing
By having different conversations, this facility improved its results.
“You were here to help us, not to tell us what to do.”
— Reliability Supervisor
“RLG accelerated our ability to put ideas into action.”
— Operations Superintendent
“The TMP™ process was the first step in a seamless execution of the project.”
— Front Line Outage Coordinator
Context/Challenge
This ammonia fertilizer manufacturer was recovering from a process safety event which caused both facility and reputational damage, along with production downtime. Their leadership was committed to learning and improving processes and behaviors to transform their cultural practices and restore strong performance.
Through dialogue and assessment, RLG and leadership priorities became:
- Assessing risk by organizing a team to assess plant health and identify bold actions to mitigate threats.
- Aligning priorities. Teams had competing priorities. We aligned and balanced metrics on safe, reliable uptime, and developed a tiered accountability to reinforce priorities and drive front-line decision making.
- Strengthen follow-through: Work backlogs were extensive and action items lacked commitment and follow up.
- Improve leadership: Both leadership skills and behaviors were inadequate, as revealed in assessment surveys and interviews.
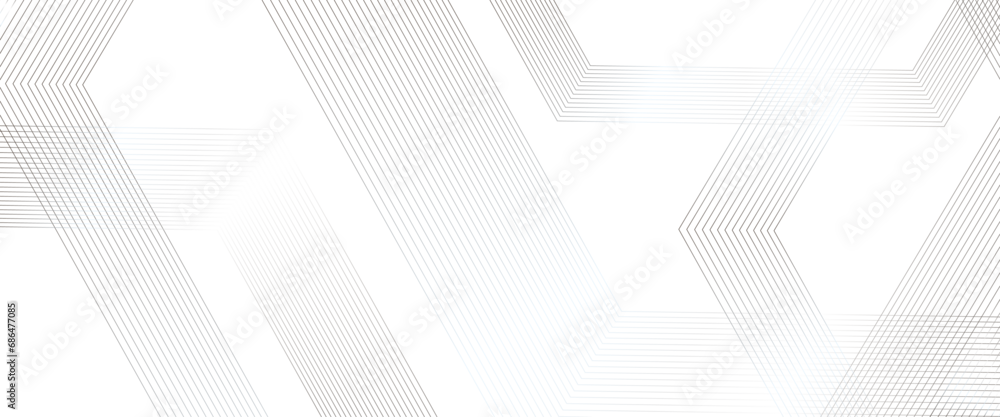
Approach
Enable the right conversations for focus on the right things.
- Inter-disciplinary teams were set-up to review, analyze and integrate diagnostic and performance metrics to determine the health of the plant. Using a systematic approach, threats and vulnerabilities were identified, prioritized, and acted upon with the required urgency. The team kept the plant informed using a detailed scorecard.
- Optimize outages: Both planned and unplanned outages required improvement in planning and execution. Improvements to procedures, systems, and actions, both internal and with contractors, created repeatable high performance.
- Communication Framework: Working closely with operations, maintenance, shipping, engineering, safety, and reliability groups, RLG established a results-based dialogue using dashboards, reporting and visual boards. These became the foundation of a powerful weekly boardwalk where accountability, recognition and front-line decision making to close performance gaps were the focus.
- Leadership Development: At all levels, through training, leader standard work, process improvement, and one-on-one coaching. Stronger decision-making with more decisions being made by front-line supervisors using data.
Result
The facility restored uptime ahead of plan, enabling a $42.6 million impact above budget.
- 30% ammonia plant uptime increase and 24% urea plant uptime year-over-year
- 7 production records set, with restored performance well-above baseline performance
- 10,000-hour maintenance backlog reduction

Ready to change the way YOUR business is done?
We would love to learn about your unique challenges. Contact our team for a no-obligations conversation or even a site visit.
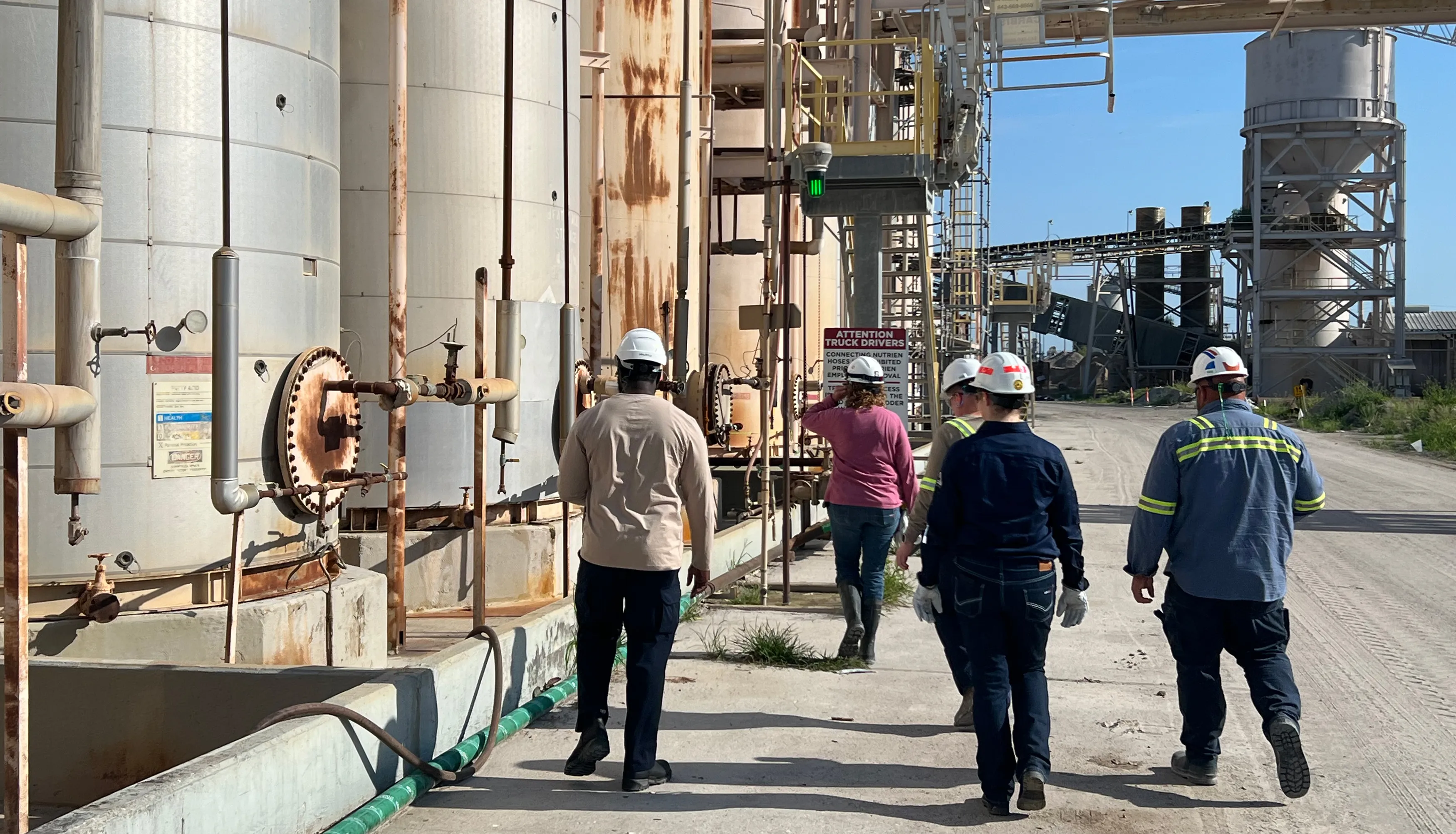