
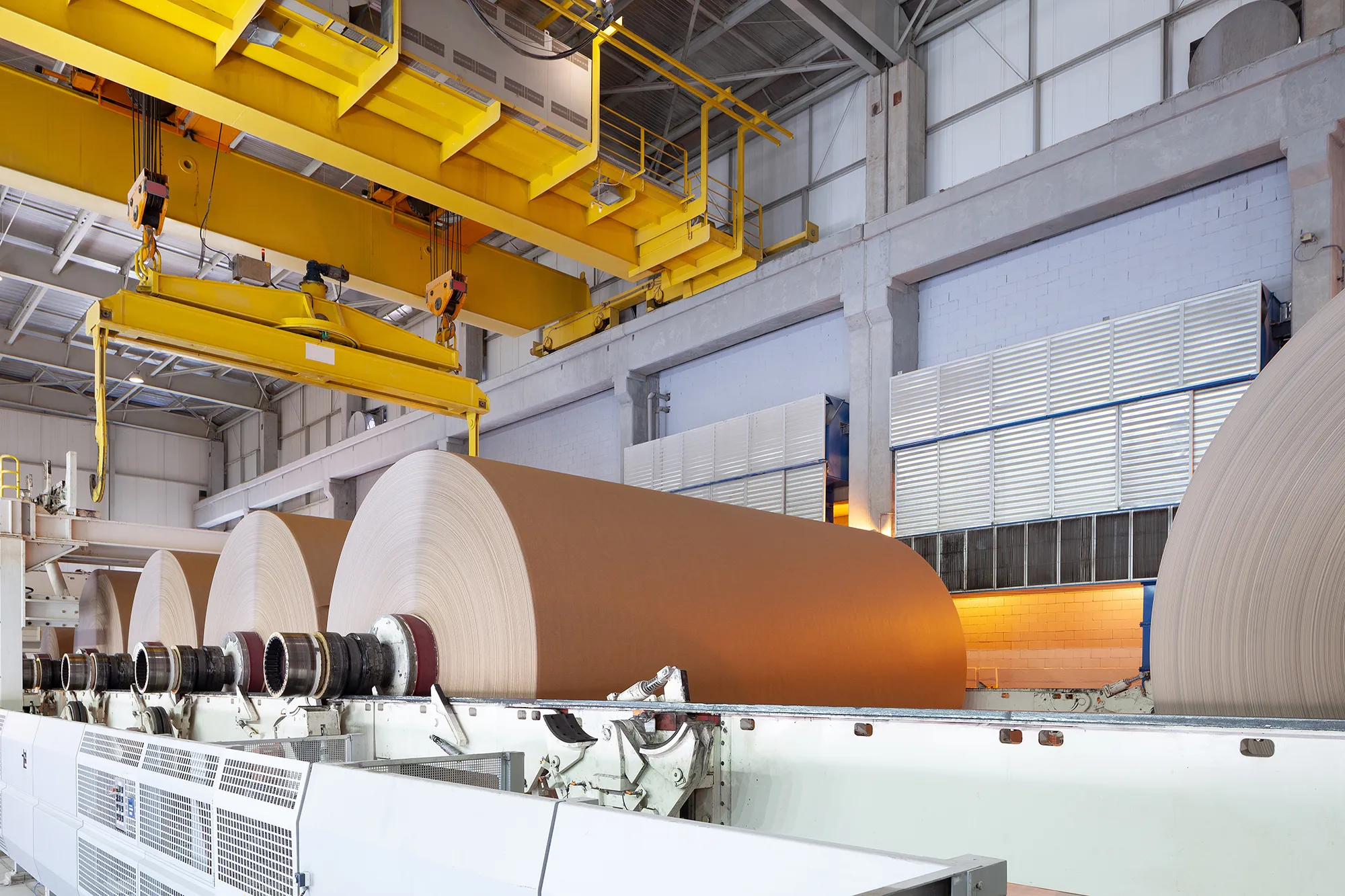
Paper Manufacturing Safety
After years of effort, the safety trend was again heading in the wrong direction.
“To have a significant impact on the safety performance, we needed to find a way to get engagement from our employees.”
—Chair of Safety Committee
"I was not sure if this RLG program was going to work at first, but I am pleasantly surprised at how well we are doing, and I am seeing a difference in our supervisors' engagement and interest. The safety performance results speak for themselves."
—The Site Manager, acknowledging both the mill safety committee and RLG’s contributions
"I am very pleased at how the employees have been looking out for each other and focusing on creating a safe work environment day in and day out."
—Safety Committee Co-Chair, after 8 Months
Context/Challenge
This kraft paper mill client was eager to improve employee safety, but after years of effort, the trend was again heading in the wrong direction.
Together with the mill leadership and a corporate mandated commitment to safety, RLG was brought in to provide systems and hands-on effort to make lasting sustainable change. Leadership decided that the key to success was to spread the safety focus across every single employee and contractor in the mill.
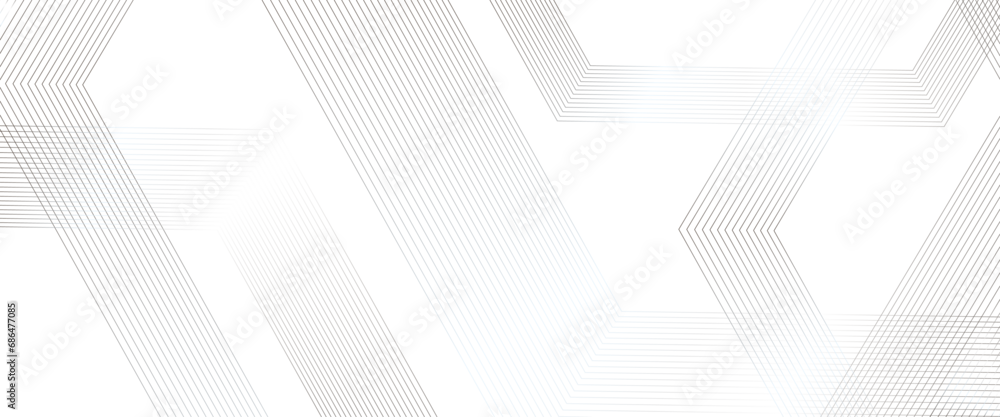
Approach
Leadership was committed to change, and together with this client’s Maintenance and Engineering Manager, who championed the safety “Courage to Care” program, a transformation occurred.
- An assessment of their current safety practices was communicated to everyone from the leadership team to the front-line employees.
- The first step was engaging managers and supervisors for their input on the approach that was needed to change safety and performance culture – recognizing the two go hand in hand.
- Implemented RLG’s Operating Rhythm™ elements to increase visibility and engagement.
- Introduced safety and recognition moments at all crew and leadership meetings.
- Facilitated safety continuous improvement teams with crew and leadership involvement.
- Deployed the 'Good Catch Program,' where all employees site-wide supported daily safety hazard assessments and continued the challenge to identify improved safety processes in their everyday work and environment.
Result
This mill and their leadership were recognized for the dramatic turnaround in performance.
- The mill manager received a mill manager of the year award by an industry association.
- The mill and its safety champion were awarded the provincial SAFEty Leadership award. Read the full article (link here) on page 12 - 14 of Pulp and Paper Canada.
- The Recordable Injury Rate improved by 65% and lost time injuries improved by 67%.
- More than 575 ‘Good Catches’ submitted during the period April to December – 85% of which were corrected immediately or through the maintenance work order system.
- High employee engagement and boosted morale.
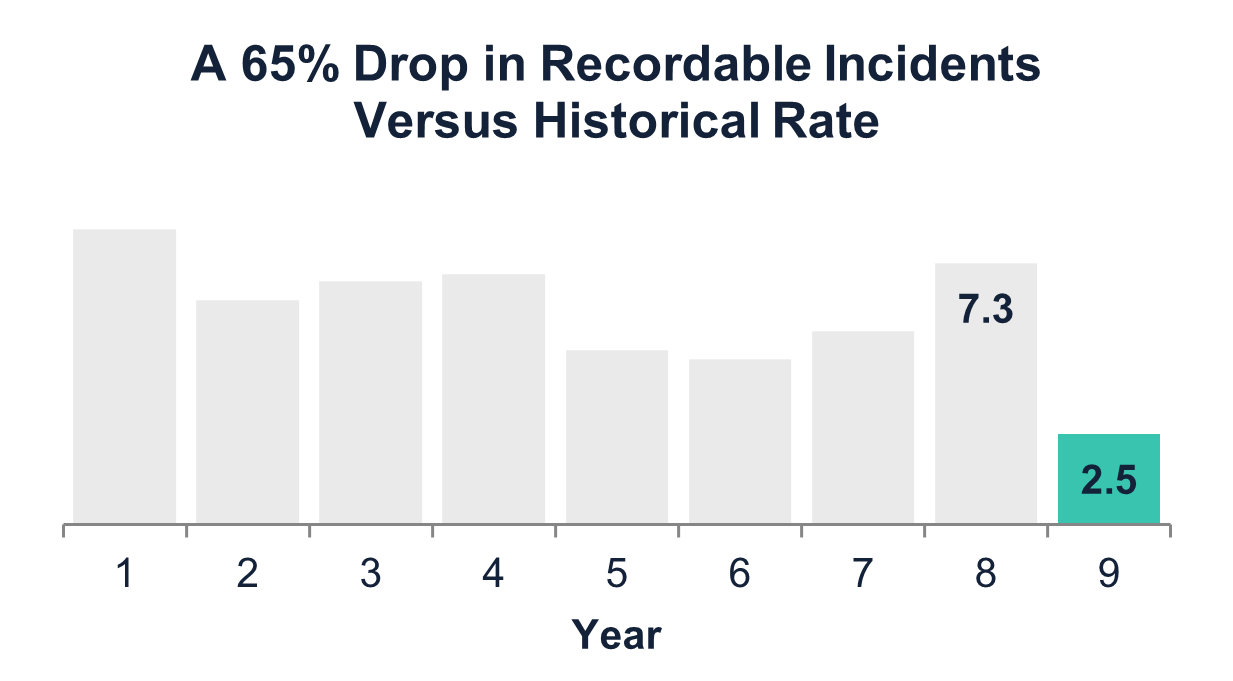
Ready to change the way YOUR business is done?
We would love to learn about your unique challenges. Contact our team for a no-obligations conversation or even a site visit.
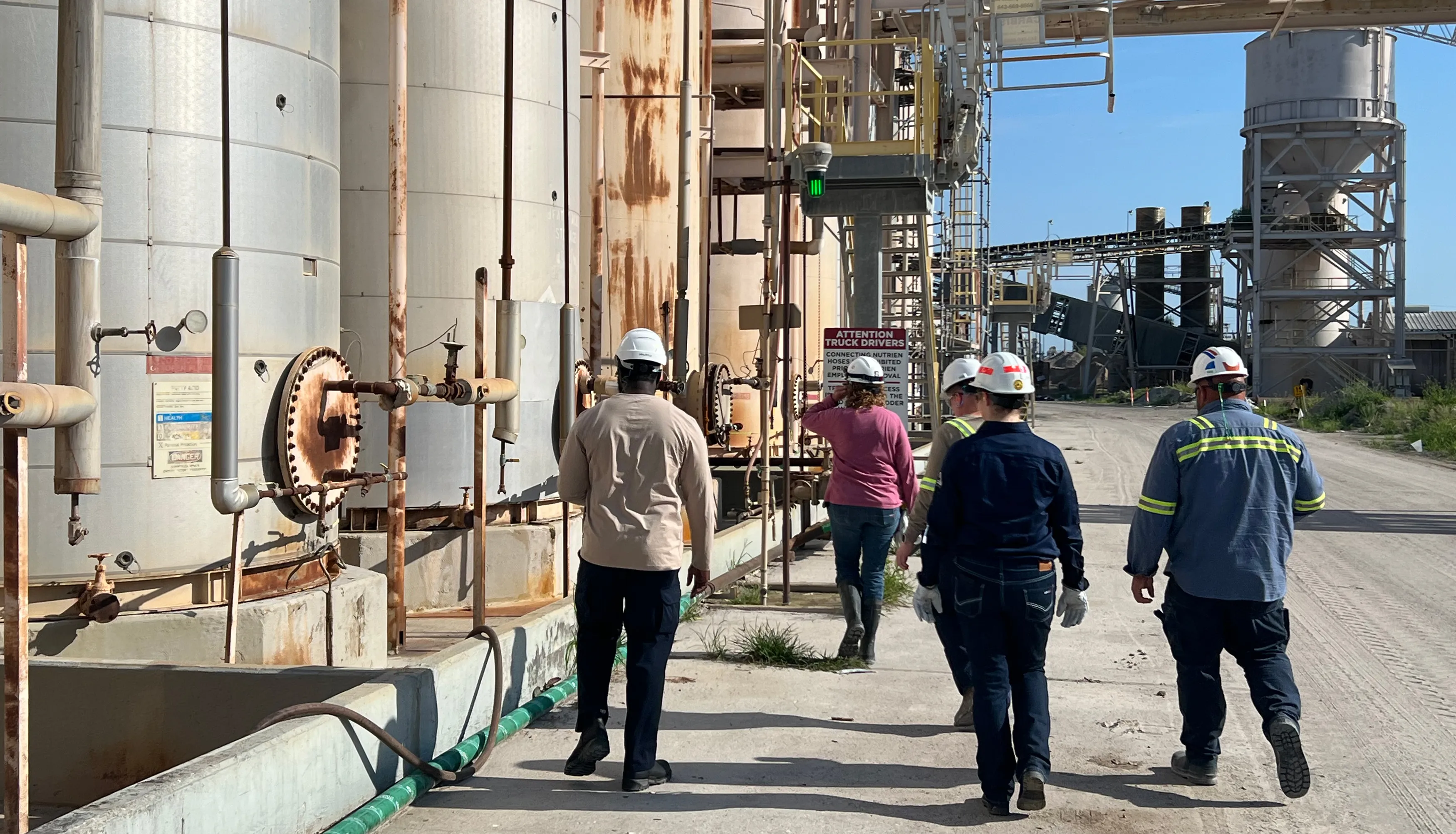