
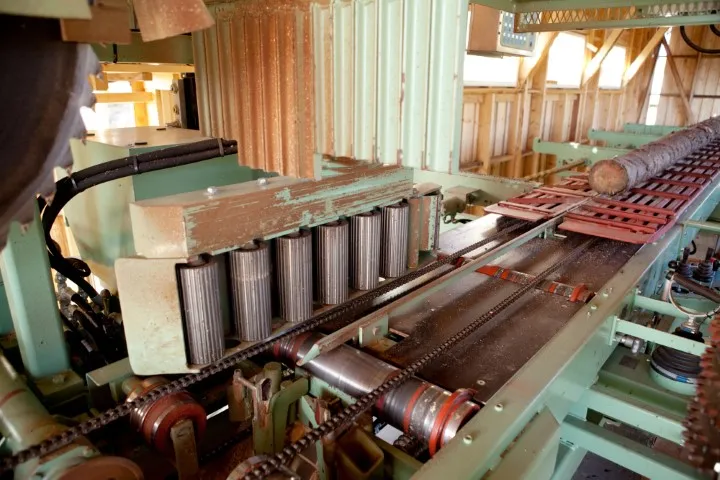
OSB mill achieves sustainable performance improvement
This single time OSB mill consistently underperformed expectations but with RLG’s help, it is now considered top of the fleet.
“Unlike my experience with other consulting companies, collaboration with RLG was very much positive. The RLG coach became a real team member and put all his knowledge, skills and energy to bring value to the team focusing on shared priorities and aligning team’s efforts to achieve improvements for the mill.”
General Manager
“We believe all of our operations run safer and more efficiently with a strong operating rhythm. RLG’s work with the entire is an example of how the operating rhythm is directly linked to the results of the organization and our business goals. I am very pleased with the progress in our facility, as well as the comfort in knowing the work and systems will ensure the sustainability of these results.”
SVP Operations
Rel
Context/Challenge
This mill consistently underperformed expectations and despite the infusion of significant capital over the years, was never able to reach their production goals.
RLG’s assessment of the organization led to four primary conclusions:
- Production had stagnated despite the modernization of the mill.
- Shutdown practices were poor, resulting in annual shutdown being consistently over budget and late. and processes leading to significant downtime.
- Poor, unreliable and underused data to drive operational decision making and maintenance practices.
- Cost management was not in control.
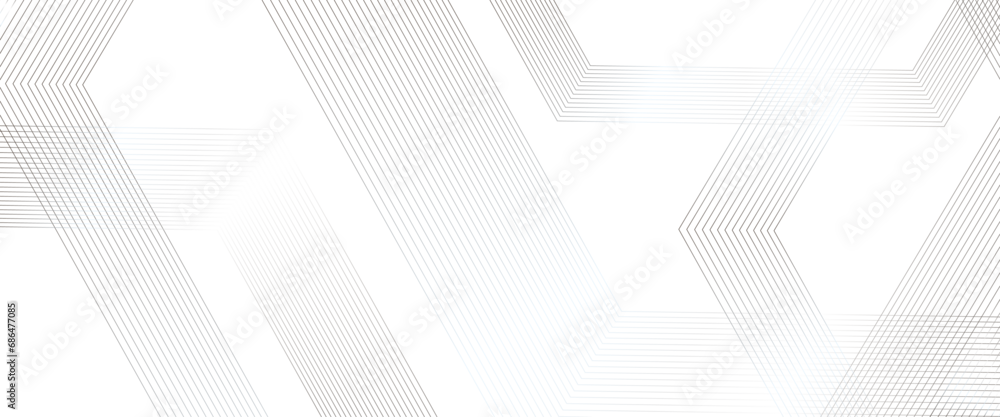
Approach
The client partnered with RLG with the specified goal of getting the team aligned to:
- Realigned business processes, tools and teams to enable production growth and higher reliability.
- Developed a strong Operating Rhythm around business goals, expectations and feedback on a daily, weekly and monthly basis between individuals and team across the organization.
- Improvement initiatives were facilitated with key leaders and front line employees to address gaps in maintenance and reliability.
Result
RLG’s partnership with this organization, helped to deliver significant bottom-line results, including:
- Press uptime grow from 92% to 94.9%
- Press speed efficiency increased from 90.7% to 92.6%
- 22% decrease in external contractor costs
- On-time, on-budget, on-scope annual shutdown for the first time ever
- Maintenance manpower utilization grew by 15%, while overtime decreased by 17%
The sustainability of the processes was in RLG’s focus from the start of the project. This was achieved through engaging all employees and leaders, connecting the teams, developing their skills and competencies, helping them with defining root causes and supporting their efforts in resolving the issues.
Ready to change the way YOUR business is done?
We would love to learn about your unique challenges. Contact our team for a no-obligations conversation or even a site visit.
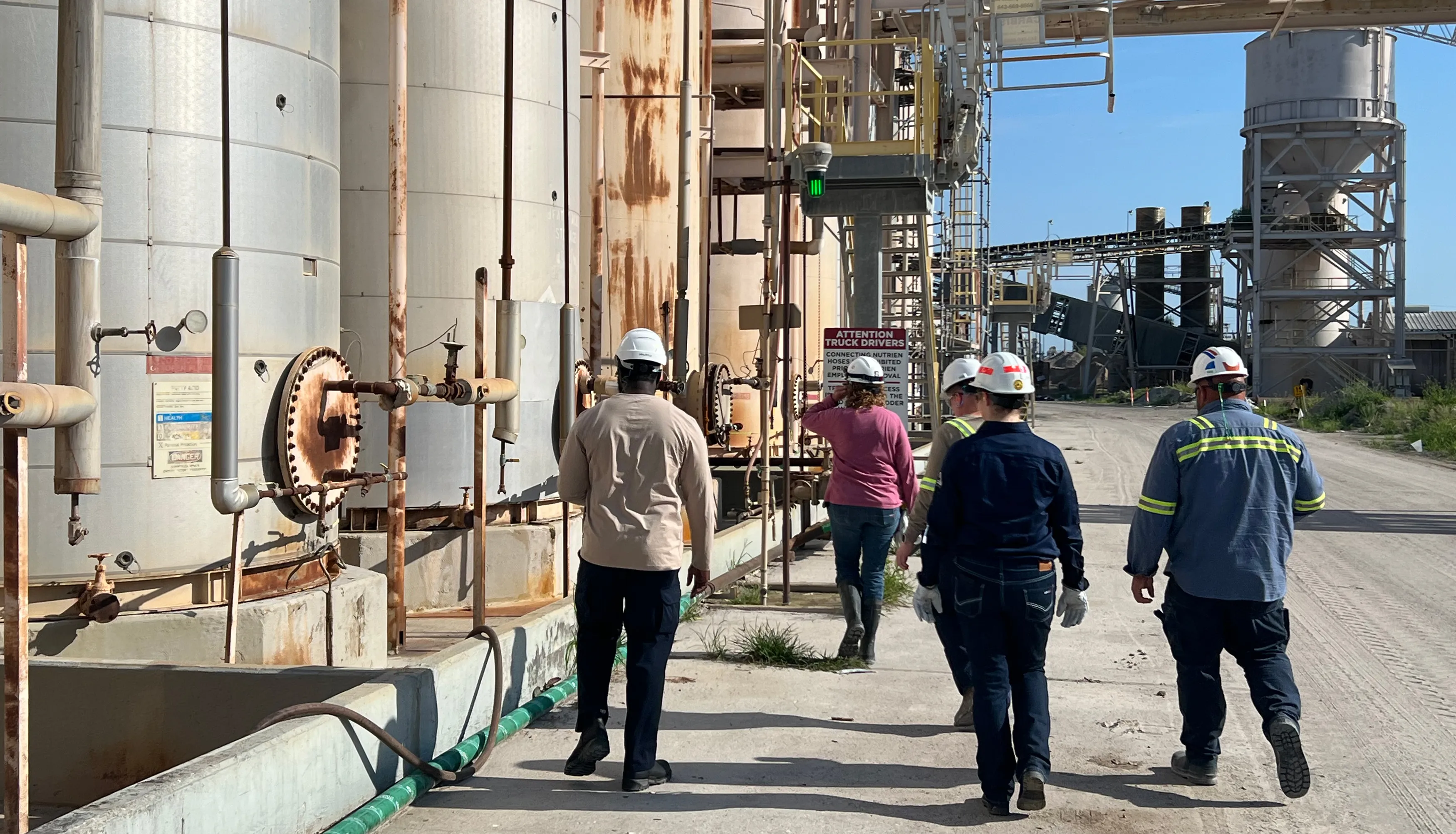