
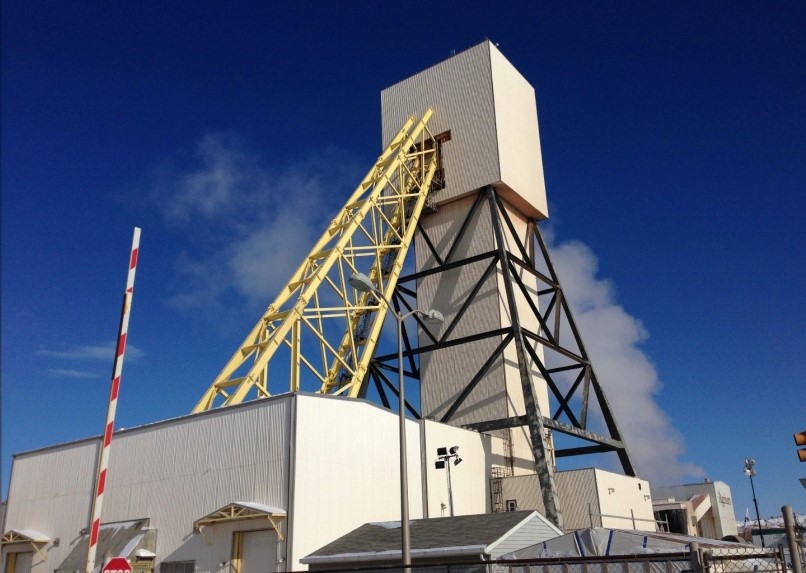
Mine Safety Culture Change
This underground mine with on-site processing was looking for a dramatic change in processes, attitudes and behaviors toward safety. With safety came improved operational performance.
“The shift towards interdependent safety means more people are empowered to act and protect themselves and others from injury. Most of our workforce feels compelled to intervene if something appears unsafe.”
—EH&S Manager
“RLG helped us transform the site leadership and accountability culture from one where business success was dependent primarily on top level management and was therefore not sustainable, to one where all levels of the organization are now engaged and empowered. In essence, they helped us connect the front line to the bottom line with one of the major achievements being a substantial and sustainable improvement in safety performance.”
—Divisional Vice President
Context/Challenge
This client, with 600 employees, operates an underground mine with on-site processing and shipping facilities. The ore body is 1,000 meters below the surface. Client leadership was seeking to dramatically change the processes, attitudes and behaviours toward safety.
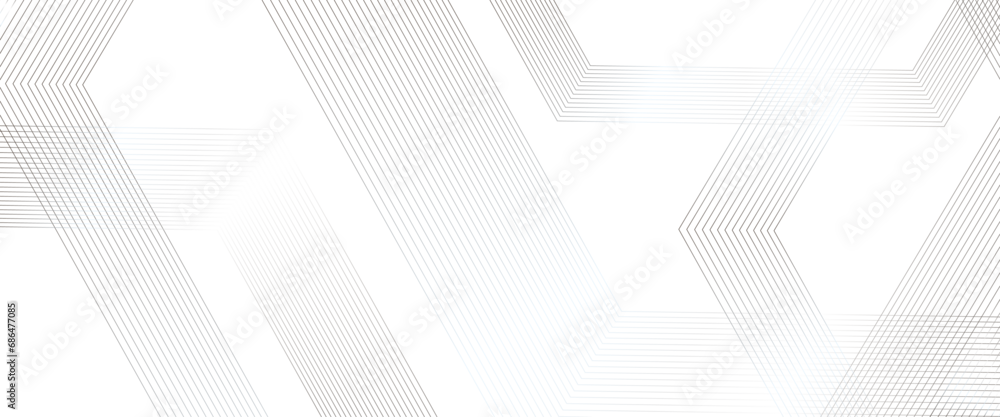
Approach
Employee safety, delivery of work and the needs of people are deeply related. This leadership team jointly focused on safety and the daily execution of work towards improved results on all site metrics.
- Focus: Company leadership declared their belief that all accidents are preventable and that a sitewide shift in focus and attention to safety was underway. This included collaboration with union leaders to create joint and aligned messages.
- Accountability: Made safety KPIs visible, both leading and lagging, down to the crew level. Increased the consistency and quality of daily safe work practices.
- Involvement: Made safety a primary focus of all crew meetings and activities. Engaged front line teams in deliberate continuous improvement activities.
- Response: Regularly evaluated progress toward interdependent safety behaviours. For nearly two years, kept focus on a methodical implementation plan.
Result
This mine, mill and loadout significantly improved performance in safety, asset reliability and cost through a combined push towards operational excellence.
- Recordable injury rate reduced by 55% and lost time injuries dropped to zero for three consecutive years.
- Consistent attention in every crew across the entire site to safety and safe work practices, with visible metrics and daily conversations.
- “Safe, reliable production at a competitive cost.”
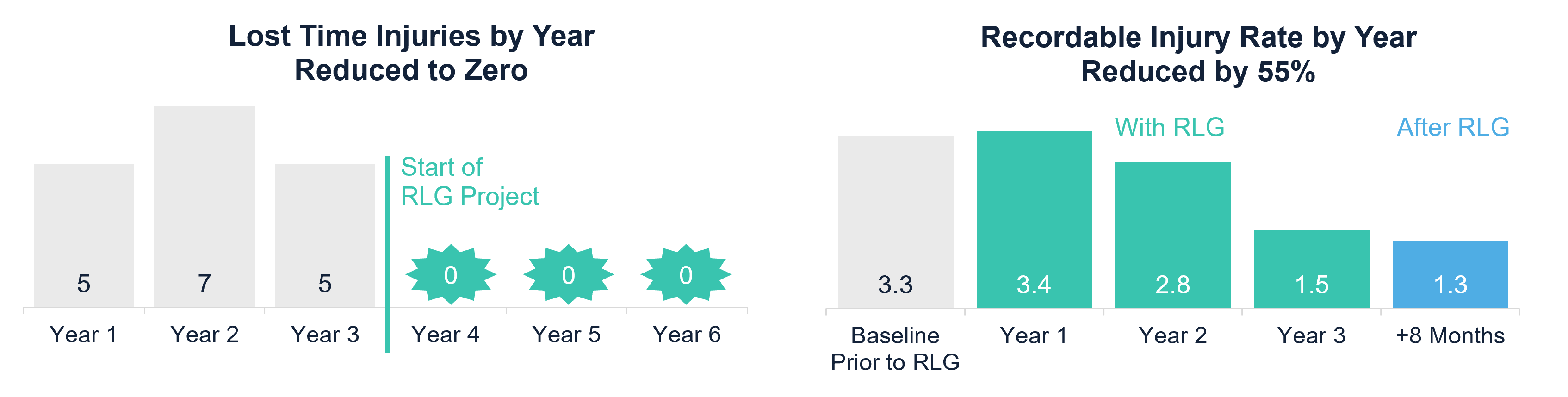
Ready to change the way YOUR business is done?
We would love to learn about your unique challenges. Contact our team for a no-obligations conversation or even a site visit.
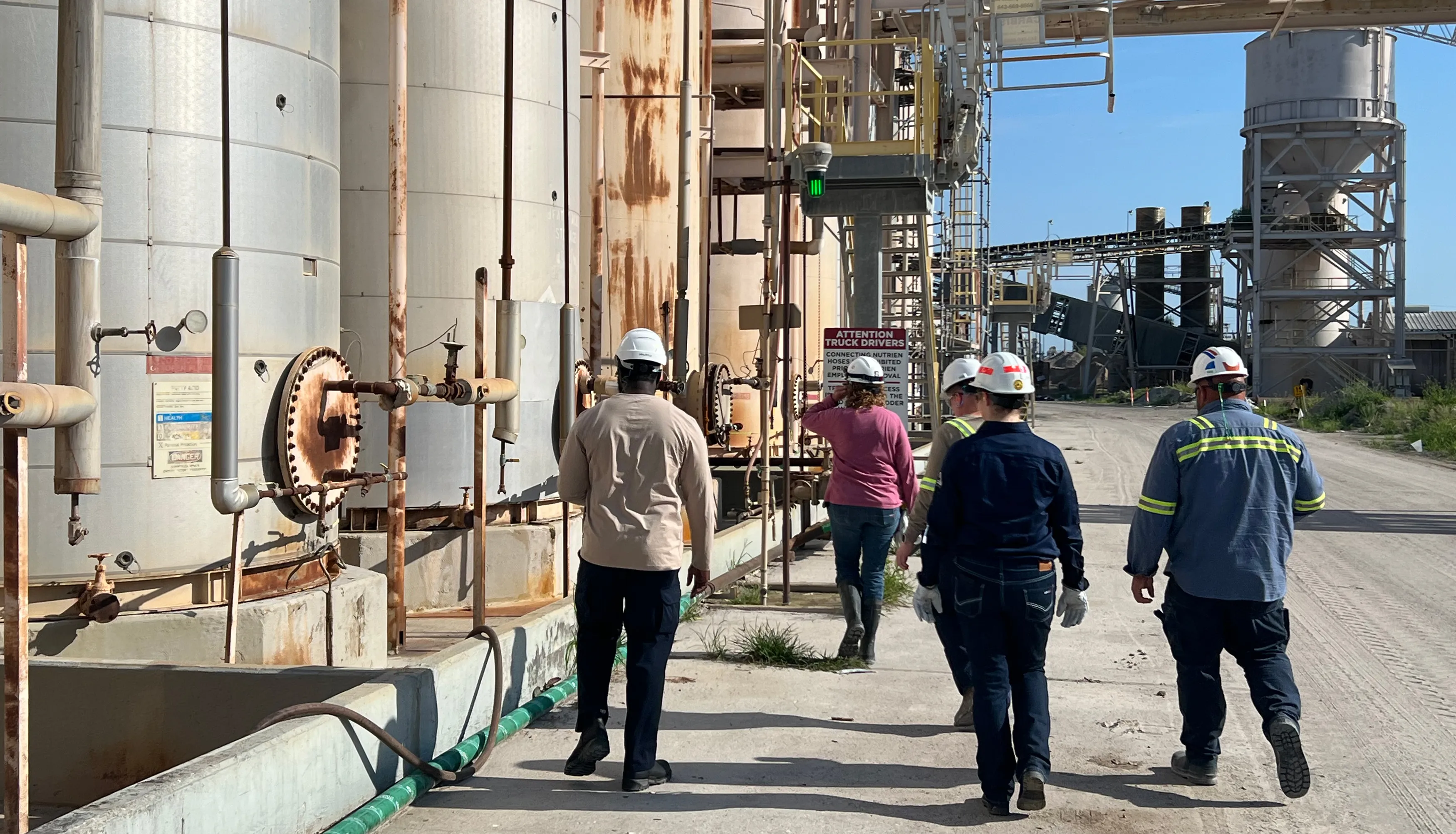