
.webp)
Changing Results Through Focused Conversations
A pipeline construction project was experiencing disappointing results and trends in Safety, Quality, Environment and Progress.
“RLG introduced their Operating Rhythm™ to provide the key interactions necessary to create a results-oriented culture. With RLG embedded in the project, they kept an eye out for ‘pinch points’ that could impact the project’s schedule or cost. RLG has the proven potential to be used in both operational and capital projects environments.”
— Deputy Project Manager, Pipeline Construction
Context/Challenge
A pipeline project was facing disappointing trends in Safety, Quality, Environment, andProgress (SQEP). RLG was engaged during the construction phase to provide frontline leadership coaching to support an initiative aimed at addressing these trends and improving SQEP performance.
The engagement deliverables were clear and concise:
- Facilitate the successful roll-out of the initiative by coaching frontline leaders and enhancing their team leadership skills.
Assist the construction team in achieving improved SQEP results through the use of RLG’s Operating Rhythm™ and TMP™ (Theoretical Maximum Performance) optimization tools
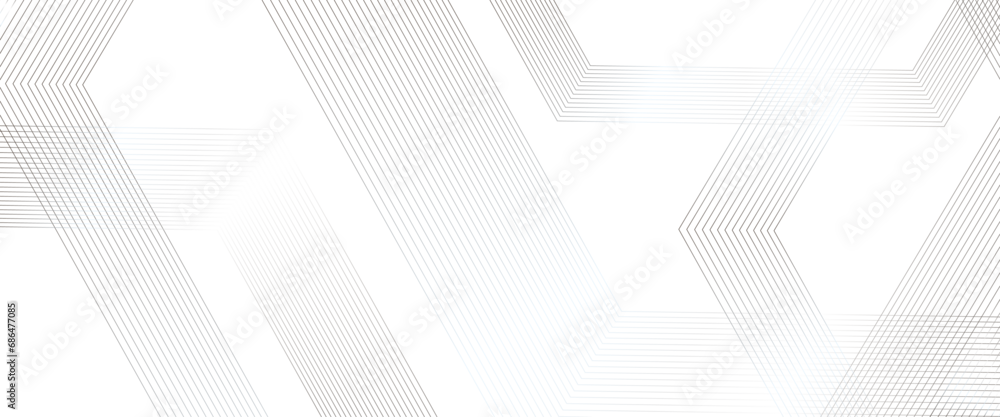
Approach
RLG deployed a rotational team to work closely with the field construction owner and contractor teams across 35 to 40 work fronts:
- Crew Talks: At the start of each shift, every crew met to identify potential hazards and issues for the upcoming day; review work assignments and performance expectations and “grade” the prior day’ sperformance.
- Business Reviews: RLG worked with the construction leadership team to establish a weekly “game plan”, a process that each supervisor used with his crew to review the week’s SQEP performance and capture opportunities for improvement in the coming week. Each Thursday, senior leadership would visit a selection of crews on the right of way and participate in this review.
- Boardwalks: Performance boards were installed in the construction offices of the two major camps. These were frequently used to facilitate consistent, disciplined communication and follow-up on safety and progress results as well as equipment and manpower resourcing.
Result
The RLG engagement helped deliver a turnaround in project results and yielded a greater than 8:1 ROI for the client and improvements in the targeted measures of safety, quality, environment and progress:
- TRIFR down 65%
- Weld repair rate down 43%
- EIFR down 47%some text
- 21-dayschedule improvement for C2/C3 closeout
- 45-day schedule improvement for facility tie-in
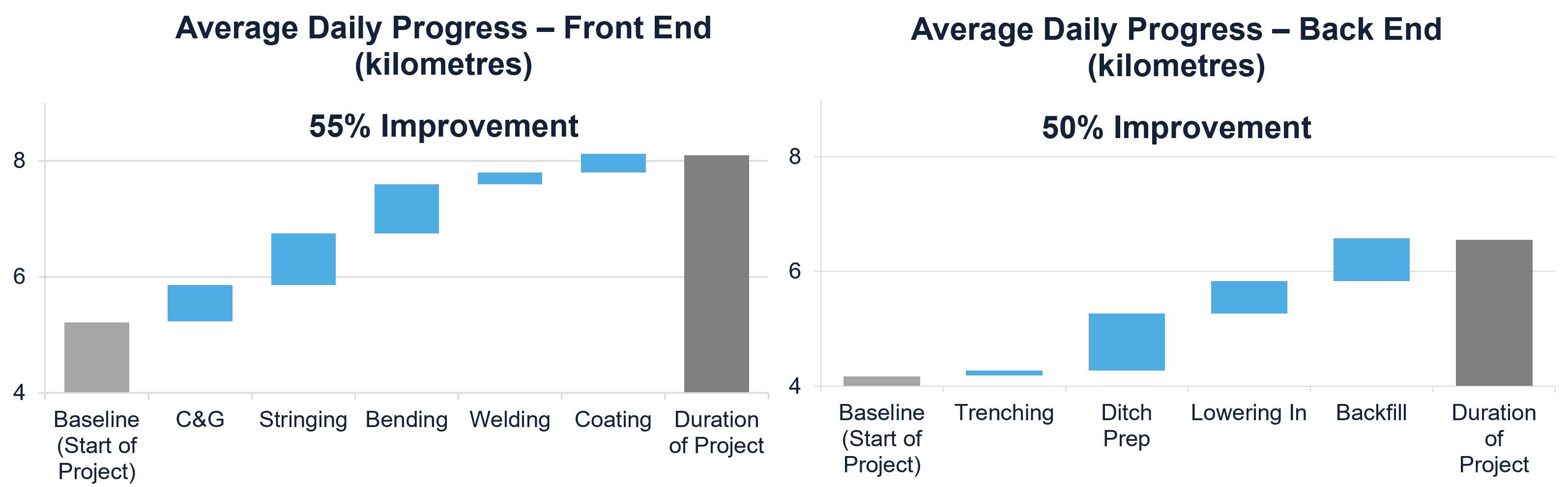
Ready to change the way YOUR business is done?
We would love to learn about your unique challenges. Contact our team for a no-obligations conversation or even a site visit.
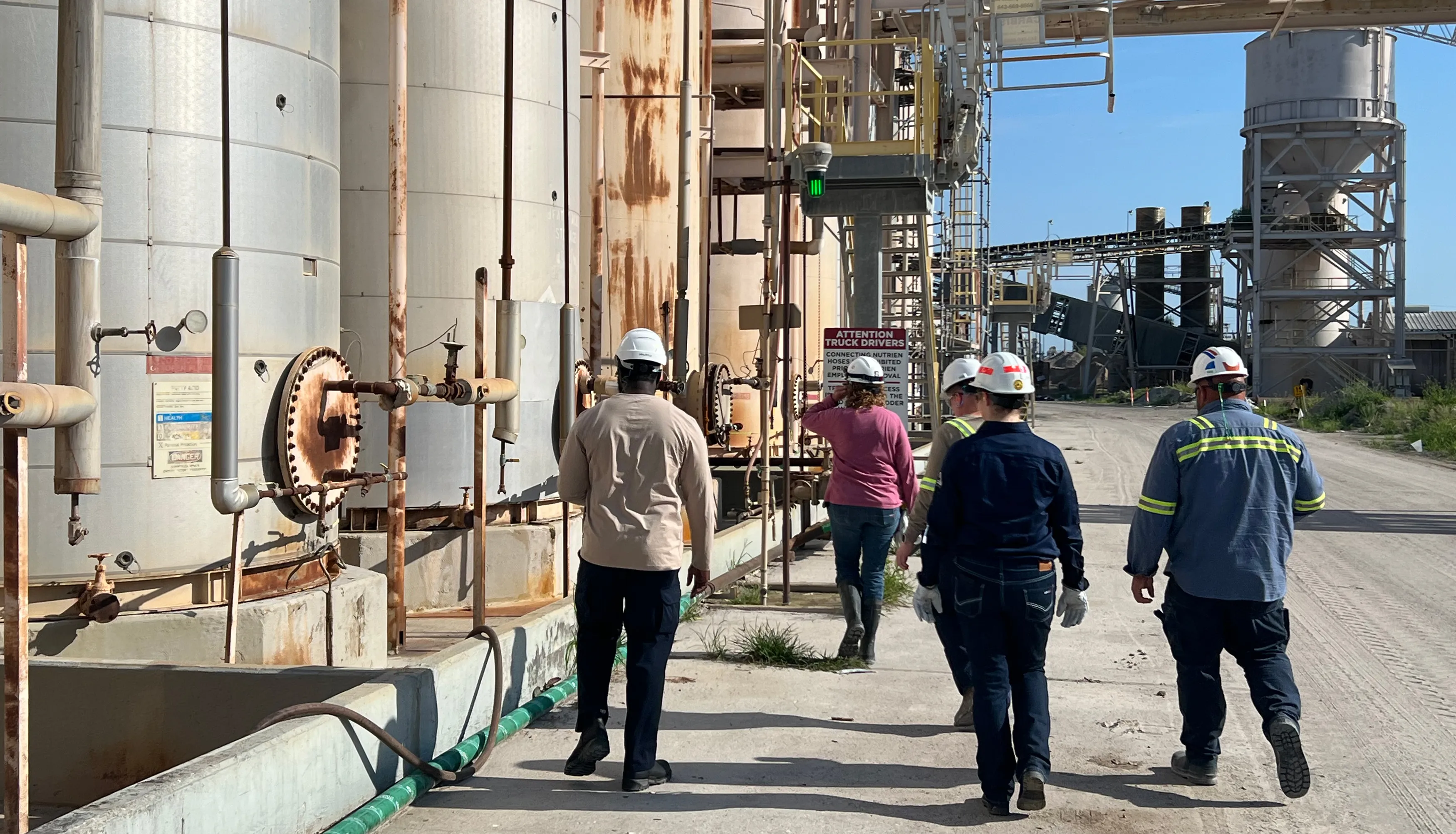